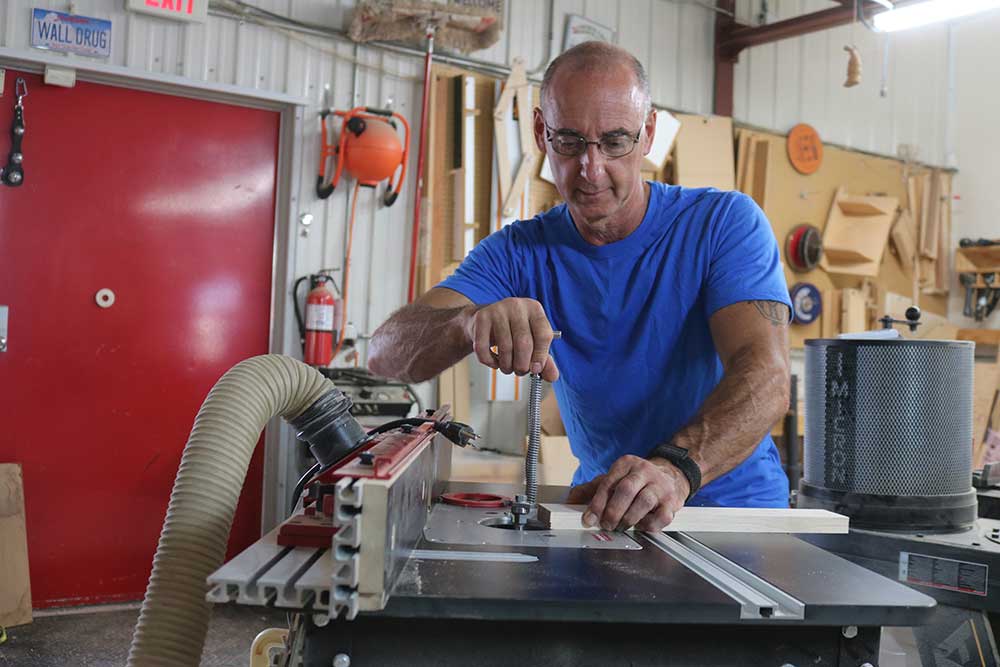
Build a Paddle Board
George VondriskaWhat a great project! If you’ve ever wanted to own a standup paddle board, here’s your chance to see what it takes to build one. It starts with a kit from Jarvis Boards.
What’s the deal with the kit?
The Jarvis kit gives you the skeleton of the SUP; the ribs and rails that provide the boards structure. Jarvis sells a bunch of different kits so you can make a board that matches your needs. Even better, if you want a design they don’t have they’ll custom create a kit for you.
Boarding the board
As a woodworker one of the most fun aspects of making the board was ripping the strips and creating the pattern for the board’s top and bottom. It’s mostly cedar, but other species were added to provide contrast. You can cut the strips yourself like George did, or you can buy them through Jarvis.
Shaping
The strips are glued to the form and to each other. After the glue is dry the board gets planed and sanded to shape. This is a VERY fun part of the build; giving the board its curves and seeing it take shape.
What makes your boat float?
After the SUP is shaped and sanded you’re ready to make it waterproof. Epoxy and a top coat of varnish take care of this.
A HUGE thank you to the sponsors behind this video:
Jarvis Boards
Bessey Clamps
Bridge City Tools
Fuji Spray
Grizzly
SawStop
SurfPrep
TotalBoat
Anybody who knows me knows that. I'm a big outdoors guy. I'm a big water sport guy. Christa and I own kayaks. We own a canoe pretty soon.
We are gonna own paddle boards. I am really excited about this project and here's the deal. I'm working with the Jarvis board kit. And what's neat about this is that they have done the hard part, which is design this so that it's actually gonna work. I'm gonna do the woodworking part which is put the kit components together and then put strips on here in order to turn what you see here into a paddle board.
So what's neat about this is there's a lot of room for creativity. I can change species here so that I get contrast. The woodworking is not difficult. It's just finesse. You gotta pay attention to what you're doing.
So, in this video, it's not about giving you how two steps because Jarvis does a really good job of that. What I wanna look at is what does it take for a woodworker? Like me to put together a paddle board? What's the accessibility level of this so that you can do this in your shop too. Now, this is a big project.
There's a lot going on. And as a result for this video, we have a lot of people involved. So for instance, we have Bessie Clamp working with us. You're gonna see as we put this project together. It's pretty clamp intensive when we're putting the strips on.
When we're putting the rails on the outside, we are gonna use clamps and glue over and over and over and over again. We've got surf prep involved. They're gonna come into play after we've shaped the board and we have to sand all the wood down to a good surface. And once the fiberglass is done, that's gonna involve sanding as well. Bridge City tools and their planes.
These are amazing products and one of the really fun things about this project is that you're gonna create a fair curve and we're gonna do a lot of that using those hand tools, using the planes in order to get nice smooth curves into the paddle board prior to that sanding step. Now, as we're doing all this work, we're gonna create some dust. So grizzly is involved and they're gonna help us keep our lungs clean. We've got a Grizzly air cleaner set up so that as we're producing dust, it's gonna grab that dust for us. We have a saw Stop Cts saw and you're gonna see a lot of ripping happening here.
We need some 316 strips. We need some quarter inch thick strips, all of our cedar is gonna get pushed through that CTS saw. And of course, what's nice there is, we've got the sawstop brake technology involved. Once we get everything cleaned up, sanded, ready for the next step, we are gonna be ready for total boat. We're using Total Boat products in order to seal the board.
First. Then over that sealer, we'll apply fiberglass mesh and epoxy in order to make sure this is a completely watertight surface. The very last step, we wanna make sure that the epoxy itself is protected. So Fuji is involved so that we can spray a nice coat over the top of those epoxy products to make sure that they're UV protected all in all. Like I said, big project, a lot of different people involved and I can't wait to get moving forward with this first step.
We are gonna meet Eric from Jarvis boards and hear about his love for this whole thing. And I am so lucky to have Eric from Jarvis in my shop today. So we're gonna meet Eric and then as we go through the day, he's gonna also help me work on a paddle board. So thanks for coming. And uh first thing is, let's hear a little bit about your love for paddle boards.
How did, how did you get here to be the owner of Jarvis Boards? Yeah. Yeah. So Jarvis Boards, I took it the company over about two years ago. At that point in my life, I was kind of in this transition from my corporate desk job to wanting to use my hands again.
Uh, I had a custom furniture shop in Chicago and I, this company had been following, uh, makes these really cool Diy Kits. Um, and so I've been a follower and fan of Jarvis boards because you were a paddle boarder. All right. It's like, kind of coincidentally you already had a love for this. I did.
Yeah. So I grew up in, in small town Wisconsin. There's a million lakes. I grew up 15 minutes from Lake Michigan, always out on the water in the summer. And then this company came up for sale and I was really excited about the opportunity because it kind of overlaps my enjoyment for being out on the water.
My love for woodworking and just helping other people bring their creations to life. It just kind of matched everything that I enjoy. And I, I really like that aspect because you're not, I don't know, you're not just a corporate type trying to sell paddle board kits. You've got the woodworking understanding that means you wanna make sure woodworkers can work with this stuff. So you've got that real world part of woodworking that you're rolling into the accessibility of the kits.
Now, the one that I'm working on this is 11 ft four, but this is one of a selection of kits that you have available. Right. Correct. Correct. Yeah, this is our most popular model.
This is our 11 4 all around paddle board. It's your traditional stand up paddle board that you see, it's got this rounded nose, basically looks like a giant surfboard. Uh We have multiple models, different sizes of this as well as a what's called a touring paddle board. And that has more of a pointed nose. It's a little bit narrower, it's a little less stable, but you can go much faster because of that displacement hull.
And the other thing we were talking about a little bit ago that I think is crazy is if somebody comes to you and they're like, well, I don't like paddle board A B or C, this is what I wanna do. You're fully set up to design whatever they want. So maybe that's, if you're a large person who needs a bigger board or whatever those needs are, you can custom design a kit for them. Exactly. And that includes outside of just paddle boards.
What I've been working on too is expanding into surfboards and wake boards. And basically the, the internal structure is the same. It's just the center spine, these rib pieces and the side rails. But I can design any water board sport, you can imagine. And we can turn it into a kit.
So, bottom line, if, if the, if the water thing you want ends in the word board, you can help them with that pretty much. All right. So, um, what we're looking at now is not, you know, this didn't just magically appear a few steps happened before this. So next thing we're gonna do is turn the clock back a little bit and look at what it took to get to this point for my paddle boards. What I wanna do is go with the strip approach, which is gonna be from the center work out with strip after strip after strip to cover this.
So I'm choosing to use cedar from that. So just first off in technique, Eric another approach would be instead of applying the strips here, a person could make a panel off the paddle board and put the whole panel on. Right. Yep. Ok.
So if you're gonna go in this direction or with the panel, um cedar for me, what are good, what other, what are other good material choices? Yeah, I would say, yeah, to your point, most people choose cedar, it's pretty well accessible and it's really lightweight and it's beautiful. Once you fiberglass, it uh an alternative would be just standard pine. I've seen people make these things out of two by fours uh from their local store. Uh There also is uh a wood called Polonia that's a little lesser known.
It's very strong, but it's very lightweight and it also is a great alternative if you can get your hands on some. So for me, one of the things I recognize is that I wanted to make sure I got good quality cedars. So I did my shopping, not at a home center, but I went to more of a man pot kind of a lumberyard and recognizing I'm looking for cedar two by sixes, the clearer, the better. Um If, as I start ripping this into strips, knots are gonna fall out. Um, we can work with that but it's harder to work with.
So, um step one was loading those up at the lumber yard. Step two was bringing them into the shop. Um One of the things I think it's important for people to recognize on the material side of this is that yes, cedar has natural weather resistance. But at the end of the day, we're gonna envelop this whole thing in epoxy. So it's really the epoxy is what creates the waterproof shell.
We don't need to lean on wood characteristics for that, which is why pine can work. All right. So then where we were at is, um, in this case, 11 ft four for my paddle board. So you gotta have a 12 ft long table to put these forms on. Um So one approach, the approach I took for this was to make a strong back and the strong back is this box down here for me, I got everything out of 158 inch thick, four by eight sheet of plywood that I did get from a home center just construction grade plywood.
And as I put it together, I used a stapler and glue in order to get everything built out into 1 12 ft long continuous straw back. Now, one of your ideas that I stole that I really, really like is um these pillars down here. So, so for you, because you, you're neck deep and all this stuff once people have the strong back and they're looking for a way to set this up, let's go other options first. What else can people do? Yeah, I mean, you can simply just lay them across.
A couple of saw horses is if you don't have, um, if you don't want to do the concrete bucket route and that's probably the most, most common way to do it good. Um So for me, what I really liked about the bucket idea is that as I'm working around the paddle board, nothing is sticking out that I'm gonna run into and remember we've still got a lot of steps to go. Um We're gonna end up sanding planing fiberglass. So when those steps happen, I think your recommendation on this was we take the strong back off and we still use those columns coming out of the buckets to put the board on. So I love the dipping, the double dipping like that.
And then two, these are, this is very easy to move if I need to slide this whole thing around my shop. Yes, it's concrete but I can move this all by myself. So I love that poured concrete concept. Yeah. Um Now that gets us to a point where we had the strong back, we had the pillars, we had the concrete.
One of the cool things about your kit is it comes in a box. It's like this is not quite, you know, but um you make it ship all by having these individually laser cut components in a box. So even the long outside rails, the long center spine are broken down into small components that fit in like a 4 ft long or so cardboard box. So the next step for me was getting the parts assembled enough that I could get the layout on the strong back. So there are a couple of steps to that.
Um I use the string on the strong back. We want that spine to be straight, straight straight. So a string never lies. So I started with the string from the string. I drew lines on the strong back that got me a line and to end then I put the center spine on there and I could strike lines from the spine indicating where each individual rib has to go.
That got me to a point where I could start getting the frame on here, which is crazy. Cool because you're now it's starting to look like a paddle board. Now you see what you're doing. Um And one of the things that was neat about that is I was able to clamp across from rail to rail. And uh the total boat tho provided a really good solution to what I was trying to do here, which was I, I just clamped everything together, made sure it was right.
And then I went back corner by corner by corner and applied that thick so on the inside corners to reinforce the whole concept. And that really leaves it as one solid structure. And so many people have said, um you're building an airplane wing, which is kind of the same concept in woodworking. We would call this a torsion box. It's um we have this internal frame, we're gluing the skins over the top.
So when it's done, it's crazy strong. It's, it's really cool. All right. So leading up to where we are right now, anything else from you, from your experience with putting these together that it helped folks out? I don't think, I think maybe one thing is just um hot glue is really good for uh getting those, those tabs down on the table.
It's just like really easy to quickly set them. Uh and you can have this whole frame pretty much set up before you do the fix. So in, in a very short time, that's an important step. So we are to a point finally, a really exciting point where we can start putting strips on to put strips on. I'm gonna make Eric help me cut some strips, um, a little bit challenging.
We're gonna rip 12 ft long, two by 42 by sixes. Um, so next thing we're gonna head for the table saw and make strips and dust. Let's do it. I'm done jabbering and we get to finally do some woodworking. So, one of the things, let's talk about cutting these strips because two different dimensions, right, that we're working with.
Yep. So, it's important to note when you set up your kit, you're actually looking at the bottom side of your board and because you're not gonna be standing on that side, you can actually go a little bit thinner with your strip. So I like to do 3/16 of an inch on the bottom and quarter inch on the top and you'd be surprised that 16th in inch across the entire board really does add quite a bit of weight. So it's, well, it's like, it's weird. It's a little number, but it's 25% right?
So, yeah, that makes sense. Um We've got our cedar ready to go. And one of the things I wanna mention too is like, you'll see as we move through this, I'm gonna use cedar and I'm gonna use other material as well because that color contrast is a cool part of this. So as a woodworker, one of the things I really like is that creative side? Like, all right, I know cedar is this color?
What if I add some walnuts, some maple, some blood wood, which I am gonna add. Um So thinking about that as you get into the kit is a good way to personalize it and make it your own um, 12 ft long stuff. So in feed and out feed support is important and you've got a great he a paddle board. H Yeah, yeah. So another great use of the strong back is if you don't have the in feed out feed, you can actually use that strong back that you built.
Uh just make sure you do, you cut your strips before you glue your frame too. And in the normal sequence, you know, not doing a video, um The strong back would still be sitting here with nothing on it most of the time. So in my case, I'm using saw horses in and out, we're gonna do our cutting on the saw staff. So of course, cool aspect of this is the brake technology. Um The other cool aspect is that we're cutting narrow stuff and I really like leaving the guard in place.
So with this saw, we can do this and with that step in the fence, I can set this so that it's right for my narrow strips getting in the right spot, but it leaves the guard over the blade. The other thing, we are gonna make some dust even with uh we've got dust collection on the saw. So this is a good time. When we're gonna kick in our grizzly air cleaner, um, in order to grab some of this airborne stuff so that we don't grab the airborne stuff. Um, you think we're ready?
I think so. All right, as ready as we're gonna be. So let's, let's make ripping happen. So, Eric, one of the things, um, so with the cedar, I got, I found it to be pretty useful in that, like pretty much every strip I cut I could use. But would, would you say people gotta anticipate maybe 10% waste in their strips or what do you, how do you, how should you play that?
I think you, it depends on the, the lumber source you've got. But yeah, if you find a piece of board and it's got quite a few knots, you're gonna have a good 10% waste. One of the things that made me think of it in that last one we cut. Um, it kind of popped a little bit as we were cutting it. It could have a weak spot, you know, a big knot right in the middle.
And when you're trying to span 12 ft, maybe that's not gonna work. It might work toward the outer edge, but you're not gonna be able to use it in the middle. So you gotta anticipate that a little. But one of the things I love about your boards is these 32 by sixes are gonna do everything. So the material requirements aren't that significant to make your paddle board.
Well, we have got a lot more ripping to do so that we have enough strips for the paddle board. And then I'm gonna make you help me put strips. I know there's a better way to do it than what I was doing. So, um, we'll rip some more strips and then we will convene back at the, uh, paddle board. This is gonna be fun.
So, uh if we do a little turn in the clock back again, we talked about the whole concept of getting the ribs and the spine onto the strong back. And then your recommendation is get one strip down the center and work out. So prior to everybody getting here, I got that one strip on. Now for me on the other board when I worked by myself, I did one strip, walked away, one strip, walk away being let the glue dry then come and do another one. Um And I love one of your tips on your video was do the strips on a day when you kind of have other stuff to do like so you could put a strip on, run to the grocery store, put a strip on, go let the dog go put a strip on because you need some glue, cure time.
Yeah, we, we want that strip to be in solidly in place before we start to work on the next one. Yes, you're gonna be repeating yourself a lot in this strip laying process. So it's nice to have some things to do while the, the Blues dry and then riddle me this batman. Um, you've done a lot of these. Do you do more than one strip at a time normally?
Yeah, I always say for the first couple just do one at a time, but you'll quickly get the hang of it and you can do two at a time and that'll, that'll twice the speed up. And I would say so experientially for me, if you can have another pair of hands in the shop, it'd be good because again, we're on 3/16 inch strips here thick. So we wanna have flutic across the top. If that gets away from you someplace, then you, you might, you're gonna have to do a lot of sanding and you might leave that way thinner than you want it to be when you're done. So, um, if you do the multiple strip thing, I think having somebody to help you see how I did that.
Um Is a good idea to make sure that everything comes out, right? Uh And Net Net, our goal is glued down and glue edge to edge. Yeah. All right. So one of the ways I did this was I laid the strip there and then I grabbed a felt tip and I wanna know on the horizontals on the ribs where, how far to apply my glue.
So I don't have a metric boatload of squeeze out over here. So with the felt tip, I just traced, traced, traced and two I would is this is a time right? For people to be looking at these strips and say like, oh that came out. So dog leg, like how much of a bow are you comfortable telling people it's ok to push against like as a woodworker, I always say, you know, you don't, you want to have a good joint inherently, you don't wanna force clamps to close it with that rule. Stick here.
Yeah. Yeah, same rules apply. I mean, it doesn't have, it's not gonna be clamped super tight. Um, but you should be able to get, uh, like finger pressure and you can see that closes up nice. Yeah.
So anything that pops off your saw looking like a rocking chair don't use it here. Um, I'm going with type on three. It's a waterproof glue. But again, in the big scheme of things, we're gonna encase this whole thing in fiberglass. So, waterproof is nice but not imperative.
Right. Yeah. Yeah, exactly. It's, uh, it's, it's a nice to have the, the fiberglass and the ox, you're gonna do the majority of that and you're, you actually dig polyurethane glue as well because, um, or tell us why. Yeah.
So the polyurethane glue has some expansive properties. So, if you do have a little bit of a gas. Oh, no, that's expensive. Ok. Uh So yeah, it does have some, some it expands and can fill gaps a little bit.
So if you don't have this perfect clamp, you know, that foam or that glue is going to expand into a foam and uh and fill those gaps, which is helpful. And two on these edges, we were just talking about this, like these are construction grade two by sixes. So if the faces of those two by sixes, which are now the edges that we're mating up here, if those faces weren't really, really flat and really, really clean when you go to close this, they may not, which is another spot where the gap filling is gonna be important because it'll help compensate for that. Um All right. Well, let's throw a bunch of glue on and then we'll go, we'll clamp it, Judd.
Let's do it. All right. Do you care? So, for me, I started in the center and then worked out. Does that jive with your thinking?
Yeah. Yeah. That's exactly right. Um And making sure that I have enough that way because I would be ashamed to get everything in clamps and yeah. So right here is a part in my experience than the other one you wanna be careful with because if you just come here and clamp it kind of forces this up.
So my point with this being work your way down toward from here to here to make sure this is even then this is even, then this is even a couple more. We're pretty much there and that leaves us like half done, right? Because we're squalls, but we're not pushed exactly. All right. A little vertical pressure.
And then you were talking before we started this about the tap test, which is what? Yeah. So some of these will just lay down really firm just with the, the horizontal clamping and to check that it's all the way down to, you could just tap on it if you hear it. Uh And there's some space in between there a bit like rattles, it rattles a little bit. Then it's a good place to throw in one of these spring clamps or the sea clamp.
All right. You happy with this looks great. All right. So one of the questions is, these are 12 ft long boards. If we don't have 12 ft stuff, that's not a deal breaker.
We can still make a 12 ft paddle board with scarfing. Correct. So, we're gonna look at scarfing. It's a cool word. We're gonna look at scarfing next to create a scarf joint.
What we need is a really steep angle like this in both parts. And when I've got that on the end of both pieces, we can overlap them and glue them together and it's surprisingly strong. So the way I'm gonna start is by making a block cut at a steep angle and I'm gonna get all of this clamped in place and then we got a little too much sticking out. There we go. What I'm eyeballing here is that angle has got to go down and end up at or slightly behind that corner.
And then a great tool for this is one of the bridge city, low angle planes. I'm using a block plane and all we need to do is just keep whittling away. And with a low angle that's important because of the way that we're shearing across that end grain. And then as I get close, eventually it's gonna get to where the plane is on here. And I'm shooting this angle onto that board.
So I just stop watch and that's about it when that's a straight line from there across there, your scarf joint is done being cut and then we can look at gluing that together to put this together, have some wax paper on your bench. It would be a shame to glue the board down to your bench top, little bit of glue, same stuff that we used on the strips and then put the scarves together. Now, one of the things you want to do is make sure this is running in a straight line. So I'm gonna put a straight edge on there, check that and then just clamp over the top done. Now, I've got one here that I did previously.
Same material. It's that same mahogany. It's scarfed right there and this is what you end up with, which is pretty crazy. Cool. I turned 6 ft boards into a 12 ft board with this scarf in the middle.
So this is pretty cool. We're setting the paddle board free these, these little pillars under there to stick beyond the form and that's what they're supposed to do their legs. So we're cutting just above the strong back. I feel like I'm in a lumberjack contest with Eric over here. Um And then once they're all free, we'll flip this over, lift off.
That's already looking so cool because you can't, you can't, you don't get to see the school curve when it's upside down. So that's um what a neat moment right there. So now we have a couple of things, we're gonna trim all of these off so that we get rid of those and we have that shape and we're gonna do this trim and um Eric's got a good point, which is, it's best to do this when you can look at it so that, you know, you're not gonna hit your outside shape there and then we just gotta get close because it's finished with a flush trim around it, right. So, um for that, if we just leave an eighth to a quarter beyond the form, a flash trim bit is gonna take care of the rest of that, a bunch more of that. And then we got to clean up the strong back because we're gonna use that as a work surface, right?
Um So we got some cutting to do and then we'll be back. So I think you're ready to foam home. So, so these accessories are, that's what's gonna receive the fin on the bottom when we're to that point, this is gonna be a handle so that you can carry it and then you've got that breather thing which is crazy cool and then that's a strap to put on your ankle. So, but with all of this stuff, when it's just the quarter inch skin, the bottom line here is you can't rely on just a quarter inch skin. So, um I'm a little surprised the foam is the solution, but that's a cool solution like um to give you some body to this thing.
Yeah. Yeah. The accessories need something to, to grab on to when you insert them and the foam is just a super, you know, basically weightless option. You definitely, if you want the board to be completely wood, you could just use some of your scrap cedar that you used. Um, just adds a little bit of weight that you'll never really see.
But also we're gonna use a router to recess this later. So routing foam is a whole lot easier than routing a wooden block. Um And it's too, it's important for people to know this is not flotation. This is just, it just is coincidentally f but it, it's what gives us the support for this. So let's hit that handle spot first.
And one of the things that happened was we, by which I mean, Eric grabbed the board and found center of gravity. So it was like pocket number nine is where you had happiness, right? So what I mean by that is like holding the board, it wasn't no heavy or tail heavy, it balanced. Well, um so that's where we know those need to go. So, Doctor Clamp, oh, you got the clamps.
You got them over here. Yeah. So let's go right there. Oh, I'm gonna add a little of this, fix up whatever you want me to do. Ok.
So we can actually probably add it to the frame. I'm gonna just stick here just because I'm lazy and it's easier. Yeah. So this is another good application for this tho product Epoxy that's mixing in the tip as we go and then across the top and the bottom as well. And then just like any two part epoxy that's gonna cure and hold that in place.
Yeah. So cut it on your fingers yet. Not yet. Oh, I should probably be doing this block while you're doing that. It's pretty good.
And you, you can leave the foam over the frame a little bit because you'll sand that flush later anyways. All right. That one's in as you're moving forward, you're gonna come back with sandpaper and knock these any little Nubs off. Then the other thing we'll need to do is sand the foam. So it's flush with the top of the frame and then this starts looking like the other side, one strip down the middle and then start working out.
I'm excited about this. I've got curly maple that I'm gonna use on the top. And when the fiberglass hits that curly maple, it's gonna look really cool. Not exclusively curly maple. In addition to the cedar, um, we're gonna take advantage of drawing time on this to head back for the other board and show you a couple of things over there.
Once we have this second verse, same as the first and then like fifth, 13th, 18th verse, same as the first, put another strip on, but wanted to use this opportunity to talk about again about the contrast here. This is mahogany. This is cedar. One of the neat aspects of doing this is creating your own custom look. So they'll end up being a handful of different colors involved with this board, top and bottom and you'll really see them pop, you'll really see the contrast once the fiberglass hits.
So at this point, um we got a lot of strips to go. We gotta finish this whole bottom, right? Doesn't that paddle board look cool? I have got strips on both the top and the bottom of the board. And what I'm doing at this second is just a preliminary sanding.
What I really want to do is knock the glue beads down so that those high spots are gone. I'm not concerned yet about finished sanding. Now, a couple things as the board comes together, one remember with those internal frame components, we had one part that was crowned over the top and then it's meeting the rail on the side. So one of the things that you have to do as you're getting ready to put these top strips on is you have to get the angles to meet. So the easiest way to do that is lay a strip across the ribs.
And then as you bring that down to the rail, you can see that it's interrupted by the rail, it can't go over the top of it because the top of the rail is still square. The easiest way to correct that is using a block plane. This little bridge city block plane is amazing. Use a block plane to knock that angle down and get the bet on that rail to match the curve on the ribs. So now the strips can smoothly make that transition and come over the top and over the top of the rail.
The other thing you may have found is what I have here, which is if there are spots where the strips didn't quite come together, don't sweat it, but fix that. Now, fix is as you're sanding, save some sawdust, grab your glue and the sawdust is very fine. So what we're gonna do is mix up just a little window. And what's nice about this approach rather than um using wood dough, commercial wood dough is that because this dust came from this project, we know it's gonna match. So dump some of that same type on three in there that's still a little too thick.
It's not bad then use a putty knife pack that in and the benefit to doing this now is we still have some more sanding to go. So, as we do our subsequent sanding steps, you're gonna clean up this little bit. I'm gonna give this, I don't know, it's only gonna take five or 10 minutes to dry and then come back and buzz the sander over this again so that you can see just how effective this is at filling in these spots even right there. There's a little crack in that knot. There's a little crack in that knot.
I'm giving some attention to those as well. Screed that off the top. So I'll give that a few minutes, 5, 10 minutes to dry, we'll come back and sand that section. So you can see just how effective that is at filling those tiny voids. Yes.
The before and after on that is pretty significant that split that openness in the seams was right there. And now it's completely invisible outside of paddle boards that sawdust and glue trick is a great thing to remember. The other thing that's important is, uh I've got good dust. Collection on the sander. In addition to that, I'm running the grizzly air cleaner throughout this process to make sure that any airborne stuff I do get is going there.
Not there. Now, the other thing that happened before you got here is strips, top and bottom, got trim, flush to the rails and then sanded. So that when I do this, which is now simulating the external rail, I'm gonna add, I know that I've got a straight line from top to rail to bottom so that those rails have a good glue surface. There's a little bit of a gap between the strips and the form rails. And I'm not worried about that because now when I put the exterior rails on, I'm gonna be bridging all of that and those are gonna tie everything together just fine for these rails to go on here.
They've got to make this bend and the bend doesn't look like much, but it's pretty dramatic. So just putting a piece of three quarter and cedar on here isn't gonna work and you don't wanna add that kind of weight. What we're gonna do is make two quarter inch strips per side. The quarter inch will easily make the bend. Adding a half inch of cedar on here is gonna give us good protection with this outside rail but not add a boatload of weight to the paddle board.
And that's important. So next step is from here to the table saw so we can do a little bit of resa to make our quarter inch rails. We're gonna do that here at the table saw, this is a process called res sawing. So the way we do that here is we've got a 5.5 inch wide board and about a three inch capacity on the table saw, this is gonna take two cuts. I'm gonna push through, flip the whole board, end for end go again.
And the distance between the blade and the fence is what's set for my final size. I'm a little bit over. I'm actually cutting it about 5/16 because then you'll want to clean up the saw marks on that and that'll get us closer to that final quarter inch when we're done. Um Other thing here is again, dust collection between the Vac on the saw, the Grizzly Air cleaner and listen to the tool, let it do the work and, uh, make the cut that gives us one of those pretty cool for the height of your saw blades set that a little more than half the width of what you're cutting. So in this case, it's a 5.5 inch wide, two by six.
So my blade is set just a little beyond two and three quarter inch so that the cuts overlap just a little in the middle, clean up the saw marks, you can do that with your sander and then that rail is gonna be ready to get glued on your paddle board. Big picture. Here's where I'm at. I've got that preliminary sanding done top and bottom. So the glue beads are off.
I'm gonna come back and do some more cleanup work and all that stuff. And again, these sides have been prepped to where we know everything is in plane here. Now, with the rail, you saw me cut from a really wide piece of cedar. what looks like a really narrow rail for this, but you gotta not get tricked by this. When you look at the paddle board right here, it looks like jeez, I only need a whatever three and a quarter inch wide piece.
But if we look at the boat in general, if I put this level on here and you can see from the center here, the uplift that's happening toward the nose and the uplift that's happening toward the tail. So what that means is, it's, you need a much wider piece to make the rails than it appears from just looking at the sides. So make sure on your paddle board, you double check that before you resa your piece. Then what I did is I laid that cedar on here and I traced it and I did a preliminary cut leaving it oversized. So that's gonna do a couple of things.
Eventually. This has got to get trimmed to this. So now there's less material there. It's gonna be a great application for a hand plane. The other thing it does is it's gonna make it easier to make the bend because now we're working with less material.
And then same with, you know, talking about the width of this piece. I can bend the cedar easily this way. But don't think that you can bend it this way to force it to follow the nose and the tail. It's not gonna wanna bend per parallel to the grain. It's gonna wanna bend down like this.
So that leaves me in a position of glue, glue, glue, spread, spread, spread, clamp, clamp clamp. When this goes on before I clamp it, I'm just double checking. Um Do I have enough on this end to get down there? Do I have enough on this? And it looks pretty good and then I have a little overhang on each side.
So I'm splitting the difference and then before you do any more clamping, what I have learned is do a double check, which is, is this gonna just naturally lay down and cover? And then this one is not. So what we don't want to do is clamp, clamp, clamp clamp and then try to force this over with this already in position because it's gonna kind of buckle that side rail. But if I do this, if I cheat it over a little now and I lay it down, that looks way better. And then same thing, I'm gonna do the same thing going this way and that it looks good.
So that tells me I'm centered all the way down just going again. Yeah, that tells me I'm centered all the way down and I can start clamping. Whoa, not a bad place to have another pair of hands because as you can see, um, that's quite the porcupine quill full of clamps that we've got on the paddle board there. But you want to make sure that you get that rail pulled down so that you don't have gaps between the rail and the paddle board. Now, here's what's gonna happen.
Give us plenty of time to dry. We're under some tension here. We're drawing that rail down. So give it plenty of time for curing on that glue. All the clamps come off, then I'm gonna do it again.
So I'm gonna have two rails quarter inch thick each on this side, two more on the other side. Once that's set, then we're gonna be ready for the next step. Looks good. I love how this paddle board is looking. Now, let me catch you up with where I'm at here.
I've got two layers of rails glued onto each side like I talked about in the previous step. I've also got the nose and the tail blocks fastened down. Now, the way that works is you're gonna make a cut across there. Eric has really good how to videos on how to handle that and then I use the total B tho in order to glue and then clamp this in place. So in my case, on this one, I'm using a lovely piece of lace wood.
Once I had that cut done, I applied my tho on there that two part epoxy is gonna do a great job of securing these blocks, clamped them on, let them cure. That leaves us ready for this next step, which is gonna be very fun. This is starting to generate a shape. I'm gonna do that with bridge city hand planes now on the rails. What we need to do is bring those down and not only flush them up with the top, but we've got this curve here.
So in the end, we're gonna end up introducing a bevel here to match the shape of the top. And that's part of what's gonna be fun here is working on that shaping component and of course with our cedar and a good quality plane, nice shavings coming off of there. So here's what this boils down to. I'm gonna do a lot of this. Um I'll stop in a little bit and we'll have another look at the nose and the tail blocks and what's gonna happen there because we can also use the hand planes in order to get our shaping on those.
So this is gonna be fun, gonna generate some beautiful curls here. So there are a bunch of things going on here doing this with a hand plane is really rewarding. You saw those crazy cool curls that were coming off of this. That is very fun to see happen. Now, what I'm looking for here is I'm getting that rail that I put on the two rails to match the curve of the top and part of that, in addition to laying it down this way is to give it just a little bit of ease on this corner.
You don't want to leave a sharp corner here. I wanna knock that sharp corner off the black plane is great for that. Now, once we're past this with the plane, then we're gonna go back to the sander and get a good finish sand on any everything. But also let's look at the nose because that is coming out so cool. My choice on this, like I said before was lace wood.
This is why the finish off this plane is really, really nice. It's really starting to pop that grain. I've got a little bit more shaping to do here. I've got to match the direction of the top here and bring that out and then the bottom is pretty much in line already. I got a little bit more work to do there, but then a little more rounding on the nose in general just to make it look more like the nose of a paddle board.
But I'm really excited about this and honestly, I can't wait to keep going with it and then see it under fiberglass. So marching orders are finish the planning, do, finish sanding and really the build part of this is about done. You saw me use a bridge city plane to bring the rails down. Once I had the bulk of that done with the plane, then I grabbed my sander and I finessed that the rest of the way down getting those rails perfectly flush with the top and with the bottom, I also use the sander to take down any big glue beads, any drips there were on these boards. Next thing is we're gonna do some finessing here.
You're probably gonna find some spots where the strips are not quite flush. Ary, they're not even, and that's just the nature of the way that the whole thing gets put together. So, because they're not even, there's also some glue residue there. So we have two issues. The glue's gotta come off and we gotta get the strips.
Even the bridge city scraper plane is really a great tool for this. With a scraper plane. There's a scraper iron in here instead of a plane iron. And what you'll see in a second is that this takes off just thousands of an inch per, per pass. So it's a really good way to just finesse what we're doing now and remove tiny bits of material to kind of sneak up on getting these flush.
Yeah. So this is what's coming off of there and you can see just from the delicacy or how delicate those shavings are. We're taking off just tiny, tiny bits of material. So that's great because it gives you really good control over making sure you don't take off more than you need to. The other thing that's nice with a scraper is that we're removing material, but we're not making dust, we're making shavings.
So you're not getting any airborne stuff. And of course, with the surf prep system that's very self contained, it's got really good dust collection on the sander. If you don't have such great dust collection, uh, scraper plane is also a great way to go because like I said, you get shavings instead of dust. So what I need to do is just keep working my way down the board and finessing these strips to get him even make sure there's no glue residue. I love that sound.
It just sounds great. It's the sound of a really good cut. All right, more of that to do for me. The best way to check the quality of your standing and planning work is to use a really powerful light set low. So it's going to rake over the surface.
This is what I'm doing with this surf prep led when you get down low and you look at the board with that light raking across it. It really shows any high spots or low spots you have. It's gonna make it really easy to control the quality of what you're doing and you can take advantage of this and use it again later when you're putting the epoxy in the varnish on. For the same reason, it's a great way to check your work. I'm probably gonna say this about 1000 times.
But when you first start working with the epoxy, make sure you read and understand the directions you want your environment to be right that pertains to temperature and dust. And there's also very specific mixing instructions. I'm applying total boats penetrating epoxy at this stage. And what it's going to do is it's gonna soak into the material. And one huge advantage to this is it's gonna prevent bubbles from being able to come through the other epoxy layers that we're gonna do later.
If you've ever used a sealer before a top coat on other woodworking projects, it's very similar to what the penetrating epoxy is accomplishing for us here. The penetrating epoxy is a very thin liquid, it spreads really easily moving this around with the Squeegee is a great way to go. We just want a thin layer on here. We're not trying to get a build like we will later after I had the Squeegee work done, I went back with a brush that was the easiest way for me to get penetrating epoxy on these side rails. I also used the brush to just kind of level out the work I had done with the Squeegee it's really important to know when to be done.
You don't want to overwork this and end up leaving more marks than you're removing because the epoxy has started to cure. Then we'll just let that cure and we'll be ready to start building up the epoxy layers. This is a really big moment in my paddle board. Build. What you see laying over the board is the fiberglass mat upon which I am about to pour epoxy.
What's cool about this? And we saw a little bit of this with the penetrating epoxy is when the wood gets wet with finish. In this case, with epoxy is when it really starts to pop. The Curly maple is showing up the walnut cedar bloodwood. All that contrast is really coming out.
So here's the thing. There's lots of great information out there about how to do what we're about to do. Jarvis boards has some great videos about it. So again, as I've been doing throughout this, this is really about how does this go for me? What do you need to be aware of?
So you need to be aware of, read the directions on your product is very, very important to understand how to use this part of that is environmental. You want your environment to be at the right temperature, you gotta be careful about the humidity so that the epoxy reacts the way it's supposed to react. This is chemistry, everything is there total boat. We'll be happy to tell you everything you need to know to be set up for this today. We haven't done woodworking in here because we don't want dust and stuff falling out of the air on top of the wet epoxy, there's some cure time here, the directions will tell you what the cure time is.
So, um again, just environmentally, you wanna be aware that you don't want a bunch of dust flying around when you do that. So I've been very careful about that leading up to this. You saw the penetrating epoxy get put up following that. What I did as I grab the surf prep sander and any place where I had big obvious high spots like drips. I sanded those down while I was doing that.
I was running my grizzly air filter to make sure that I was keeping the environment clear. And again, it's all about dust and not breathing it in and not leaving it in the air and all that stuff that gets us about to a point where I can mix up epoxy and get going here before I do that. One of the things I wanna talk about is this cool business with a decal with a logo that you can put onto your board. And I really gotta thank Eric at Jarvis for this tip. I saw him doing this and I wasn't sure how he did it.
So I asked and the reason I'm putting a glove on is lesson learned. You don't want to touch the mat with just naked fingers because you can leave oil from your fingers on there. And that might show up as a spot where the um epoxy doesn't want to stick very well. So you'll see, I'm gonna put this wave on the board. I love this.
Um This is printed just from my regular laser printer on rice paper. That's the key to this. when the epoxy hits the rice paper and gets it wet. The paper part disappears and you're left with just the ink so big. Thank you to my daughter Jenny for doing this drawing for me.
The wave and the sun. I think it's very cool. It's gonna actually end up under the mat so we can do that part right now. The other thing that happened after sanding is the whole board got wiped down with denatured alcohol to make sure there wasn't any dust left on there. Now, kind of like, I don't know, unmaking a bed.
I know that the mats laying here just right. So I'm gonna be a little bit careful about how I do this and then this is gonna get centered and up toward the nose and then we can bring the mat back and I'm watching it just to make sure that as I readjust, we don't lose position on that thing that gets me in a position where I'm ready to mixy boxy. So again, follow the directions I am using Total Boat's high performance Epoxy on this with their slow hardener. It's a 2 to 1 mix and again, follow their directions. So this gets about three minutes of mixing.
I'm gonna dress my mat just a little bit more. We're ready to go environmentally. One more thing. There's plastic on the floor. You're gonna get drips and I don't mean me, you're gonna get Epoxy drips coming off the board.
So you wanna have plastic down so you don't end up with that product all over your software looks great. Love the logo. Thank you, Jenny. Love the working time I get from the total boat product. So now all we gotta do is watch it, try and next couple steps, a little more epoxy work, we'll talk about that some more later.
A few things have happened since the last time you saw a paddle board here. The last thing that I did was put the fiberglass mat and the high performance epoxy onto the other paddle board. This one is a step ahead of that. On top of the fiberglass mat, you then do a hot coat and again, it's the total boat, high performance epoxy. So when you look at this, this is why it looks so amazing is because that high performance epoxy has been applied and itself levels and the board looks absolutely incredible.
Now, the next thing we need to do is get a UV resistant varnish over the top of the epoxy. So leading up to this step, a couple of things happened, you can see that the accessories are installed. So this is my handhold in the middle of the board that's gonna make it easier to pick up on the back end of the board. There is a ankle anchor so that you can tie on the board so you don't lose it. And then there's also a vent that's very important so that the board can ventilate.
Um It's very smart. It's a one way vent. So it lets air out, does not let water in when I installed those, they went in with thick. So this is the same stuff you saw used when I put the whole frame together to hold the frame together. So what's amazing about this is, it's epoxy.
It's two part epoxy. It mixes in the tip and basically we're cocking and gluing these accessories in to make sure they're gonna stay and make sure that they're waterproof once they're installed. So the thick so worked really well for that. Now with the epoxy, the epoxy by itself is not UV resistant. So the product that we're gonna add to that is gleam.
That's a spar varnish that does have UV block to it. So that now goes over the top of everything that we've done. We're gonna put that on with the Fuji HV LP sprayer. So gleam can be brushed, however, you can't beat the ease of finishing that we get from an HB LP like the Fuji system. We're almost ready for that.
But in order to make that happen, we need to scuff this just a little bit. So with its high gloss that it has right now. Yes, it looks amazing. But we want to give it just a little bit of tooth to make sure that the varnish is gonna stick. So I'm gonna grab the surf prep sandpaper 320 grit and I'm just gonna lightly scuff the entire board before we get to the varnish up.
So that's where I'm at right now. Um I love looking at it, but we got to knock this gloss down in order to get adhesion for that varnish. So I'm gonna mask up. We're gonna run the Grizzly air filter and let the scuffing begin. Well, I think I'm there.
So when you look at it now, especially when I'm down here looking at it like this, you can tell that we've knocked that high gloss off of it and that's what we want. We wanna make sure that that varnish can adhere. So I think we're pretty close to being ready for varnish with the scuffing done. The next thing I did is I masked off the accessories so that I don't end up with varnish all over those easy peasy. Let's talk about uh getting the gleam applied for a second.
Like I said, you can brush that gleam on if you want to. I love using an HB LP. Anytime I'm doing, finishing, it's such an easy way to get a great consistent coat on stuff. So what we've got here is a Fuji HV LP system HV LP is high volume, low pressure. One of the big benefits to this is clean air coming from the turbine.
So I'm using a turbine to provide the air, not an air compressor and then also the ability to control how much air I'm providing so that I can correctly atomize whatever I'm spraying, whether it's varnished today, paint, tomorrow, shellac the next day. So it works very well for that and you'll see in a second, minimal overspray. So doing that spraying in the environment we're in is not gonna be a problem. The other thing when it comes to finishing, that's very beneficial is having a low, high intensity light so that you can look at that light glancing across the surface and make sure you're doing an OK job. So I've got surf preps led, set up just a little higher than the plane of the board.
So I'll be able to get down and get funky. I'll be able to get down and look at the board as I'm going to make sure that I'm laying on a consistent coat of clean. So I think we're ready to go. The other thing I'll mention is that um after scuffing before we got here, I also wiped the board down to make sure that there was no, um, residual dust or anything left on it from the scuffing step. Read the instructions on the gleam.
Can you can wanna build up multiple coats of varnish on the paddle board or canoe or boat or whatever you're doing. Um, so read the instructions about time between the next overcoat and the next coat and the next coat. So I am going to try to be patient and, uh, do a little waiting here and then build up my coats just like I'm supposed to. The next thing we're dangerously close to getting paddle boards on the water. It's a big day.
It's time to take the paddle board for a test drive. You can see how easy it is to handle the board with just that single handle in the middle and off I go. This is the moment the whole build is leading up to. This is kind of a labor intensive project. But when this part happens, you get on the board, it's floating like it's supposed to, it's handling great.
It's doing everything it's supposed to do. This is the payoff. This is the magic moment of making your own paddle board. Ok. Ok.
This was a very fun project for me. I would do this again in a heartbeat. Part of what's cool about this is, it's so different from furniture making or cabinet making. It's a completely different type of build and it's just refreshing to do something. OK, perfect.
Part of the premise with this video was for me to go through the experience and then let you know how did it go? What did I learn? So let's talk about that and uh I'll fill you in on how this whole thing went for me starting with the kid. I love the Jarvis board kit. It went together very easily.
The support from Jarvis is really, really good. They've got instructional videos out there. So step by step, you can watch those videos and see what do I need to do next? Where am I going with this? So I have zero problems with the K aspect of this.
Remember that Jarvis makes way more than the board that I built. They've got a lot of different designs. So um have a look at their website and that's gonna help you pick out the board that's best for you. So the kid aspect went great prep and strips. I love this part.
Um I enjoy going and picking out my material. I enjoyed cutting the material, the saw stop table. So I handled this very, very, very well. Now, if you don't want to do this stuff, if you don't want to make your own strips, you can get the strips prepped for you. Um But making the strips was a cool aspect for me because as I cut strips with both the cedar and the maple and the walnut and the blood wood.
I was starting to see what this pattern was gonna look like on the board. So that is a woodwork is very fun for me to compose my own. Look for this paddle board. But like I said, you can get strips made for you. You can buy strips if you don't wanna prep them yourself.
The material doesn't have to be perfectly clear, but it can't have huge knots in it. Um One thing I would do differently if I did this again. If you're familiar with Whitter King, if you're familiar with Resa and book match, when you cut two pieces and they lived face to face, when you open them up like this, you have a book match. If I did this again, I would keep track of my strips and I would then put this strip here and this strip here so that working from the center out, you would have a mirror image going each way on your board. That would be very, very cool.
Um I didn't think of that until I was too deep in to go back and do it. The other thing to keep in mind, talk to Jarvis about this, you can panelize the build, which means you can put all the strips together as a panel and then put the whole panel on. So that is a different approach to working with the strips, a different approach to making this happen. Now, you've got the strips fastening the strips. My Bessie clamps were great for this.
I love the one hand clamps um because they're one handed so I could hold apart, manipulate the clamp. Clearly. I used a lot of spring clamps on this for hold down pressure. Um So I have a lot of clamps on hand. Slow and steady is the watchword here.
You gotta be patient in my normal woodworking projects. I might glue and clamp something And in 30 minutes, 45 minutes take the clamps off, set the something aside and then use the clamps for something else with this. The type on three were great, but you really got to allow time for the glue to cure, especially when you get to where you're really forcing those strips into a curve. You gotta allow ample gluing time. So um I think the way Jarvis talks about this is like do the strip glue up on a day when you've got other stuff to do so you can put a strip on, walk away, put a strip on, walk away.
When I started on the strip fastening part. I was doing one at a time because I wanted to get a feel for the process. Once I got more comfortable with it, then I was doing 21 on this side, one on this side, glue them, clamp them and then go do other stuff. Um But just be prepared for that to take a while because you're gonna wait a little longer on this to remove the clamps than you might on other Wooder King projects, sanding and planing. So, um the surf prep sander had great dust collection on it.
I ran the grizzly air cleaner while I was doing that to keep my environment clean. All of that worked great. Ran Orbit Sander and the three by four sander worked really, really well for smoothing this out and getting rid of whoops. Um The bridge city planes were wonderful because in areas like the rails are a great example where I had a lot of material to take off. The plane is faster and it's making a shaving, not dust.
So good dust collection like I picked up from surf prep and grizzly is a must. But if you can do is the more work you can do with a hand plane like the bridge city planes. Um, the better this is gonna go because you're making shavings, not dust. And like I said, you're taking material off faster, the scraper plane to knock glue beads off to level strips out. Really was a big time saver um, to save me sanding time.
So, um a little bit like putting everything together on planing and sanding, take your time. This is a very, very fun step because you start to generate the curves and as you're developing those curves, you start to see what the paddle board is gonna look like and that's very, very cool. That's a blast with the epoxy. The Total B products work great for this. Um Anytime I talk about epoxy, I say about a million times, read the directions, read the directions, read the directions.
Customer support from Total Boat is great. If you got a question, give them a call, read the directions. Your environment has to be good for this. Meaning not too cold, not too hot there. You can't have dust filtering out of the air when you're putting the epoxy on.
So one thing I would do differently if I did this again, I would get an extra pair of hands on board. Pun intended, um, accidental pun there to help me with the epoxy because there's just a lot to do. There's a lot of real estate to cover here and it would just be a lot easier if you had another pair of hands as you're working through that. So be patient with it. Follow the directions about, um, the number of coach you need to do the waiting time between coach.
Can't be too little, can't be too much. Um, again, follow the directions, talk to Total boat. They'll walk you through it with the varnish. It's kind of the same story. The gleam varnish handled wonderfully.
The FGHV LP for that was a wonderful device. If you can't spray, you can brush the gleam on. But again, read the directions because, um, there's information about the number of coats you can do in a day, drying time between coats, how to clean it up, obviously. Um, so with the varnish again, you want your environment to be right? And one thing to be aware of there is the gleam dries slowly.
So when you're doing that aspect, when you're doing that step in your shop, you can't be woodworking in your shop. Probably because if you're making dust, it's gonna settle in the wet varnish. So, um, it's another aspect that's um got, there's a lot of time involved. There's a lot of labor involved. But um the end result is really good and of course, we need the varnish to protect the epoxy.
Overall. This project was a blast for me. I really learned a lot. I really enjoyed composing the look of my paddle board and that comes down to working with the strips and making that happen. Um I like that much more than the idea of going out and buying somebody else's wooden paddle board because this is uniquely my own.
Uh the decals are up there that I put on. That's a very cool personalization step. It's labor intensive without question. But the result is incredible. And I've had so many people compliment the look of the board.
Um Now that it's done and you can't beat the first time I got that on the water and I stood on that thing and it floated and it paddled and it did what I needed it to do that was so rewarding and worth every step of what it took to get to that point. I would say this project is not a difficult project. You probably need to be not, you could be an intermediate level woodworker. You gotta be comfortable using tools, you gotta understand woodworking processes. You need to be methodical about it and just think through A then BB, then C and again, the support from Jarvis is very good on that.
Um So like I said, it's not a difficult project but you need to be methodical about it when this is all done. Um My board weighs 45 pounds finish. Um You could see in the video where I'm putting it on the water with the handle in the middle, it carries like a suitcase. It's very easy to get it to the water, get it on the water and peddling. It handled great.
I really couldn't ask for any more. So overall, would I do this again? Yes. Um It was a lot of fun. I learned a lot.
I really enjoyed seeing it develop as I went and like I said, I would say intermediate level woodworker, you don't need a boatload of tools, you need some space. Um I love the uh Jarvis idea of the concrete buckets with the pillars. Um I, that's how I would do this if I did this again because that makes a beautiful work platform. Overall, excellent experience for me. I really enjoyed this and I love to see your board when you're done.
This was one of the most detailed SUP builds I've seen so far, and a huge thank you for this. I've been wanting to make a wooden surfboard for a while now and this video was inspiring.
you never mentioned doing the bottom. Is it a repeat of the top?
Great videos like always ...what kind of blade you use to rip your strip... thanks
Hello George. I have just finished watching your video regarding the Paddle board project. Quite impressed and excited to see the entire process. Thumbs up to you about the detailed descriptions and video quality.