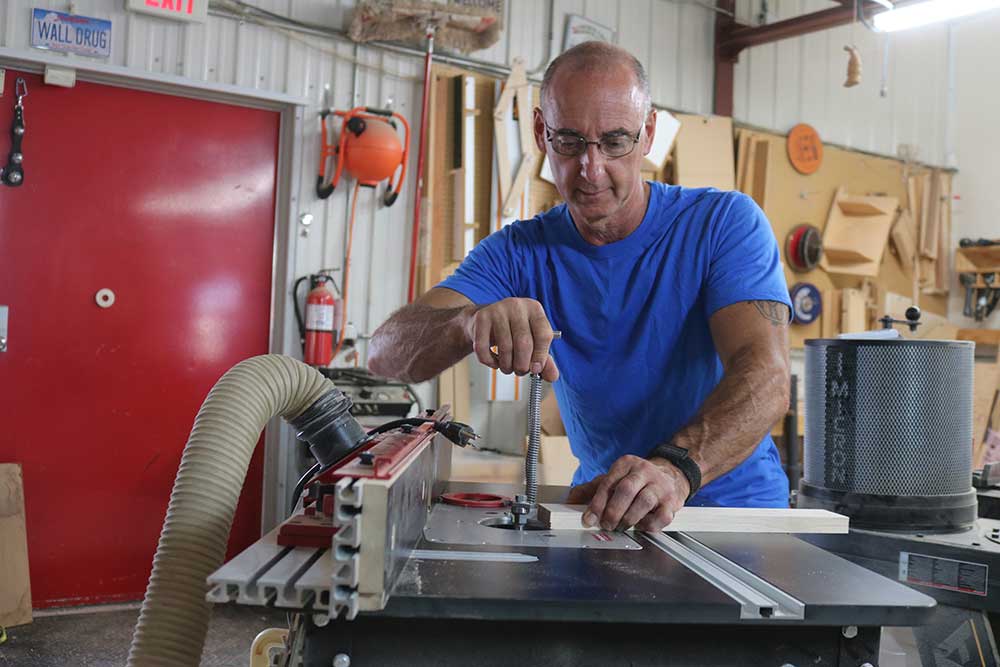
Build a Veneer Lid Box
George VondriskaDescription
Cut list:
– Ends ⅝” x 5-1⁄<sub2” x 4-⅞”
– Front and back ⅝” x 5-½” x 8-¾”
– Bottom ¼” x 4-13⁄16” x 8-1⁄16”
– Lid ⅝” x 5-¾” x 9”
Joinery
All the joinery can be done on the router table. Cut a 5/16” deep by ⅝” wide rabbet on the front and back using a ¾” bit. Be sure to use a backer board to prevent chipping. Use a ¼” bit to cut the groove for the bottom, which is also 5⁄16” deep, ¼” from the bottom edge. Do this to all four pieces, keeping the rabbeted faces of the front and back down on the router table. The rabbet in the lid is ¼” x ¾”. Be sure to test the fit to make certain the lid fits on the box. Cut a ¼” x ¼” chamfer on the top of the lid using a chamfer bit.
Assemble
Sand the inside faces and assemble the box. Double-check the dimensions of the bottom before installing it and gluing the box together. Standard yellow glue works fine for this.
Veneer the lid
If you get a mixed pack of veneers, you’ll have lots of species to choose from. Leave the lid and veneer oversize and cut them to size after the veneer is on. Be sure to use wax paper between the veneer and caul when you glue them up.
More veneering
If you enjoyed this project, check out our veneered-face clock.
More info
For more information on Titebond products, call (800) 669-4583 or visit the company’s website.
This is a great, little box. It's very easy to make. The real bullseye of this is that amazing-looking lid. We're gonna do that by veneering the lid. Now, the benefit to using veneer is that there are so many different veneers available.
And the box I showed you is made out of poplar, cherry, and walnut. They're cool-looking. But when you get a veneer pack like this, there's all sorts of funky stuff, including dyed woods, in here. So it's really a nice way to add a unique touch to whatever it is you're doing. For the one I'm gonna do now, I have a beautiful piece of curly sycamore, I think.
I'm not 100% sure what the species is, but look at the curl in that. So it's a great way to turn that plain-looking piece of poplar into a really cool piece. So simple stuff here. Yellow glue. Now, one of the things I'm doing is making sure, there was a little piece of dust right there.
If there's anything on that substrate that can telegraph through the veneer, it's gonna telegraph through the veneer 'cause the veneer is pretty thin. So you wanna make sure the surface is clean. What we're doing is just gluing wood to wood. So yellow glue is a great choice for this. Now, dimensions for each of these project components are gonna come as we're going here.
So you'll see this lid dimension a little bit later in the video. At this stage of the game, we want this to be oversized. It's not gonna get cut to its finished size until after we have the box in our little hands. When I put the veneer on, I'm making it flush with that edge. That's just gonna make the next step easier.
Now, we need a caul. We need to clamp this. And if all I do is put a clamp on that veneer, it's so thin, there'll be pressure there and pressure there, but there wouldn't be uniform pressure across the whole thing. If I do this, piece of plywood, there's a good risk that if any glue squeezes out, I'm gonna glue the caul to the veneer. So intermediate step is wax paper.
Stole that from the kitchen. Don't tell anybody. Then the caul. Now, same, make sure that that caul is dead flat. Otherwise, if you have whoop-de-dos in the caul, high spots, they're gonna telegraph into the veneer.
Then turn this into a clamp porcupine. With veneer, in this kind of press application, there's really no such thing as too many clamps. Let's have a look at our box. In my case, cherry and walnut. And I like the contrast that creates.
Two ends, a front and a back. Got my walnut ends. The dimensions for those ends, right here. That's how big to make those. Front and back, got those cut out of cherry.
They need to be this big. So cut those. Joinery is simple. Rabbets here, and then there's a groove that holds the bottom in. We can do all of that on the router table.
So let's go there next. The depth of the rabbet that we're gonna cut, the size of the rabbet, the size right here, I'm already set up for that with a 3/4-inch straight bit in the router table. It's only the front and the back that get the rabbets cut. Make sure that you use a backer board so that as that bit exits, it can't chip out the exiting side of that cut. I already did test cuts to make sure this setup was right.
What I was looking for was depth of the rabbet, which I already gave you. The width of that rabbet needs to match the thickness of our ends so that when I put this together, the end grain of the cherry is even with the face grain of the walnut right there. I need to do a bit change. This is a two-bit operation. So I'll do a bit change, and then we'll come back for another cut.
Now gotta cut grooves so that the bottom of the box has something to go into. Dimensions of the grooves right there. Need to do that to all four pieces. Potential mental mistake: Make sure the rabbets on these pieces are down when you cut the grooves. Grooviest part of the project is done.
Let's put it together. Before you assemble, you wanna sand all those inside faces because it's real easy to get to them now. It's not gonna be easy to get to them later. Dimensions of the bottom. But make sure you do a test fit with the bottom before you put glue anywhere to make sure everything is gonna play nice together.
All right. Yellow glue again. I'd like to have a clamp going this way. And that makes sure that those ends are closed against the rabbet shoulders. Make sure the top and the bottom are flush.
Then you can go thusly and thusly. And with that, we're gonna watch glue dry. However, I prepped parts ahead of time, so I am gonna grab the box on which the glue is already dry, the lid on which the box is already dry, and we'll talk through the next steps. This one's dry, this one's dry. Let's get those to play nice together.
There's a great example of why one would use veneer. That's birdseye maple, but it's been dyed purple. Isn't that crazy cool? So with your box, what you'll do is sand the outside, get the excess glue off of there, get that all cleaned up. Here are the dimensions that the lid should be.
Those are theoretical. What you wanna do is measure your box that you made. We're gonna take this dimension, add a quarter of an inch. Gonna take this dimension, add a quarter of an inch. And it's important that you do that so that the lid fits well because your box may have come out a little bit differently than the one I've planned here.
So in order to make sure the lid fits the way it should, you wanna work with dimensions from these. Once you've got those numbers, what we're going for is an eighth-inch overhang on each side. That way when we have the lid on there, there's a little lip sticking past that you can grab with your fingers to get that off of there. So once you calculate those dimensions, cut this to size, and then I'm gonna meet you at the router table. Cut the lid to size.
Size of the rabbet that goes on the bottom of the lid, right there. Here's what you wanna do. You wanna actually kind of sneak up on this being the right size so that what we're after is that when the lid goes on here, those shoulders, into the box. If you overcut it, it's not horrible, but the lid will be really wiggly on the box. So what I prefer to do is cut the rabbet a little bit too narrow, and then check it and see.
And when you look at it in this direction, right there the shoulder is in. Right there, you can see how much the shoulder's projecting past the box, past the inside. And that tells you how much more you have to take off. So then you can move the fence back a little bit, cut again, move it back a little bit, cut again. Sneak up on the final fit until that drops right in there.
So do that until the lid is a perfect fit. What you may find as well is that maybe you need two more passes on the long side and only one more pass on each end in order to get that perfect fit. So just finesse your way toward that. It's not a bad idea when you cut the lid to cut a piece of scrap at the same time exactly the same size. And you can do test cuts on that scrap here at the router table.
Finalize that fit, then we have one more router bit change to do, and we'll come back and finish out the lid. Move the fence, make a cut, move the fence, make a cut until, it's all right, you have a fit, just like that. And like I said, test pieces are worth their weight in gold to make sure you get that just right. Now, in the router table, I have a 45-degree chamfer bit. And what we're gonna do is just run .
And I'll show you part of the reason that we're doing that. So what I like about that is, especially with a darker colored veneer like that, that chamfer creates a frame around it and really increases the contrast. That if we just let the veneer run to the edge like it was, then you don't see that so starkly. Let me do a little bit of sanding, and then I'm gonna meet you over there, and we're gonna have payday on this project in just a second. Payday is .
The walnut and the cherry already look good together, but when you get them wet with finish, wow. I'm spraying lacquer. So as a result, I've got an exhaust fan running, I've got fresh air coming in. Wanna make sure you do that anytime you're working with lacquer. This is gonna be the really cool spot.
Are you ready? Are you ready? Are you ready? I love that. And man, that's got some three dimension to that curl.
It's got a really, really neat look to it. Simple project. Fun little box to have to put your special stuff into. And that veneer adds a really cool touch.
This a great project for a beginner like me. I don't have a router, so how would I build this? What joint would work here? Thanks
Even though you say to use a back for a push block to prevent tear out on the router table, after you make the first cut there is no back board there any more to prevent it or is it the sides that still support there is what is helping. Thanks, Alan
But how do you cut it to size with the oversized veneer? That was the part I was most interested in. The ends had overhanging veneer that couldn't safely butt up against a table saw fence...
Whenever you add veneer to a surface ( Especially a piece of solid wood) you have to add a piece of veneer to the opposite side to “Balance” , the panel. Not doing this will make the panel warp and twist out of shape.
Were the bottom grooves unglued for expansion? Not needed because the box is small? Wood they be glued or nailed if the box were bigger and holding weight like a tool box?
This is a great use of veneer, I have found a simple way, thinly apply glue to both the lid and the veneer, let it dry and activate both glued surfaces with an ordinary household iron.