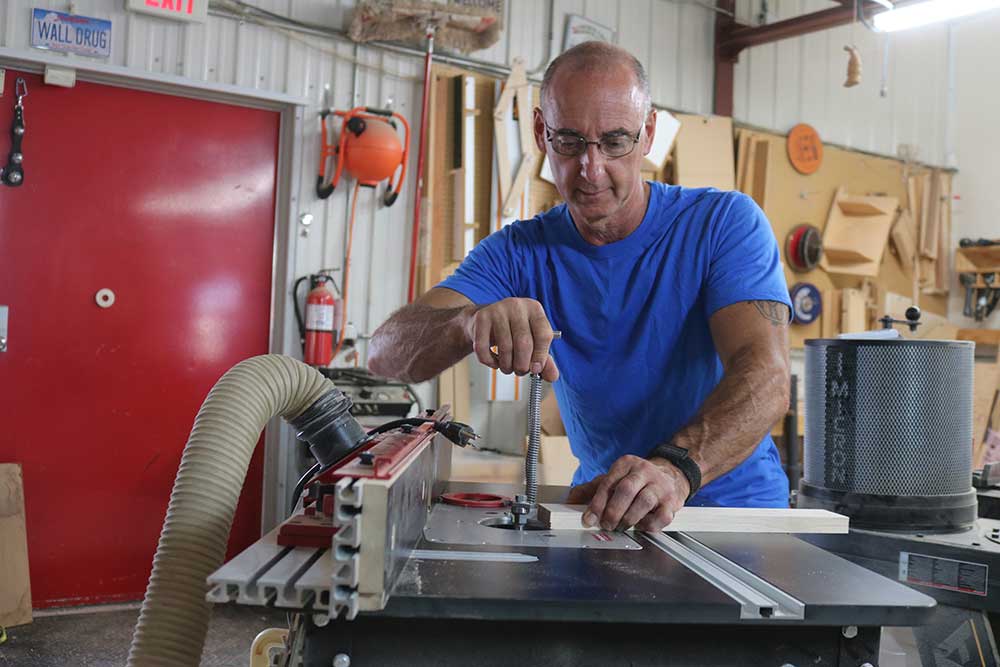
Easy Pocket Hole Joint Assembly
George VondriskaDescription
Pick the right screws
It’s very important that you choose the right screw to assemble pocket hole joints. There are lots of different screws you can use on your woodworking projects, but you specifically want to use pocket hole screws for this application. Pocket hole screws cut their own thread path and have pan heads that help reduce the likelihood of splits when the screw bottoms out in the pocket hole. Choose the right threads: fine threads for hardwoods, coarse threads for softwood or man-made materials.
Glue or no glue?
Yep, you should definitely glue your pocket hole joints. We did a little experiment to verify this. An extra-thick glue is the best choice.
Assembly
You HAVE to clamp your parts together before driving any screws. Because the hole is drilled at an angle the parts will tend to creep as you drive the screw if they’re not securely clamped. One way to align the parts, and keep them aligned, is with a face frame clamp. For larger projects, like big face frames, a bench clamp system works much better than a single face frame clamp.
We've shown you how to make pocket holes, and it felt like a good idea to show you how to put together pocket holes. A couple things involved here. One, remember that when you drill a pocket hole with most jigs, that hole ends up in the material at about a 15 degree angle. Because the hole's at that angle, the screw's gonna be at that angle, and when we drive it, there can be a tendency that causes these parts to creep. Gonna show you how to overcome that.
An important aspect of this is using the right screw. We wanna use pocket hole screws. Come back. And the reason for that is that, on a pocket hole screw, you've got a pan-head here, not a flathead like most wood screws you have, and there's a thread cutter at the bottom of the threads here. So the deal with the pan-head is that when this screw hits the bottom of the pocket, it's just gonna stop.
It's gonna seat against the bottom of that pocket. If we did that same thing with a flathead screw, they're wedged shaped down here, and when that hits the bottom of the pocket, it's gonna act like a wedge, and it's gonna tend to split your material. With the thread cutter on the bottom of the tip, that's gonna pull itself, it's gonna cut itself into the mating piece, so we don't have to pre-drill that. That's really important. The other thing that's important is choosing the right thread within the category of pocket hole screws.
These are fine thread pocket hole screws. We would use fine threads for red oak, hardwood, like I have here. We would use coarse threads for pine, softwoods, man-made materials. So that's the line in the sand. Fin threads for hardwoods, coarse threads for softwoods, or any man-made material.
On my material, I mark out where I want the mating piece to go, it could be somewhere in the middle like this, or maybe it's just flush with an end. And then in my work, I always put an X on the side of the line that the part is going to cover. So in other words, that's gonna go like that. I do put glue on pocket hole joints, and we've got this whole business covered in another video. Align with the joint.
Now at this stage of the game, if I try to just drive these screws, this is gonna go bad in a bunch of different ways. There's no way I can keep these parts aligned or in place while I'm driving that. This clamp is a pocket hole assembly specific clamp. It's got these big anvils on it, and when I squeeze that onto my material, like that, what that does is, it holds everything in registration. So that's what's gonna keep this face flush no matter what angle I'm driving the screws at.
Then from there, we simply drive. And you're set. This works, I find, on smaller scale face frames, because you really gotta be able to do what I just did here. You gotta be able to stand this up, get the clamp on there. And you can imagine if the face frame was as long as this work workbench, this is all gonna get awkward.
For bigger face frames, I really like this insert plate. This is a Kreg product, this is a Kreg product, and this is nice, not just for pocket holes, but just for general work on my workbench, anytime I wanna hold stuff down. The way this is gonna work is, we're still gonna use glue. Get this component in place, bring this component to it, to our alignment. And then when I do this, I want that pad to bridge the joint, just like that.
So just intuitively, you're gonna understand, if I have a really large face frame, it's gonna be much easier to do on a bigger work surface like this. It doesn't have to be a four by eight bench like I have, but any larger work surface that lets you clamp these in a horizontal position is gonna simplify assembly of those larger frames. That'll take care of assembly on your pocket hole joints. Very useful, very versatile joint to use, but you do wanna make sure you're putting 'em together the right way.
What is the impact of drill speed when driving pocket screws?
What kind of torque setting do you want on your drill when driving pocket hole screws? Thanks
Preventing glue from marring surface of the joint?