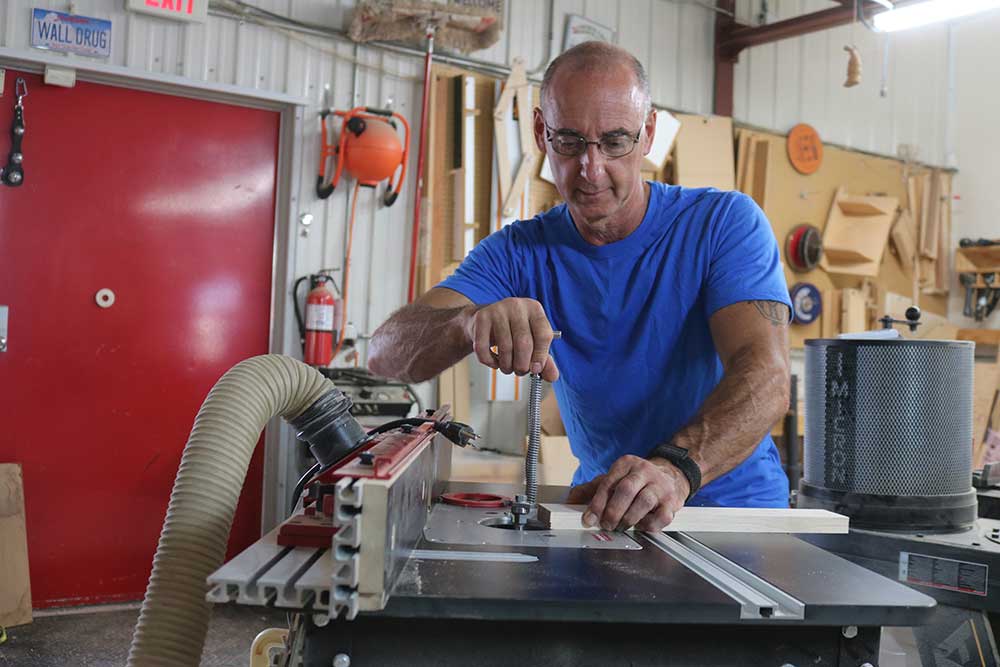
Finding Sanding Solutions
George VondriskaDescription
Tool actuated vacuum
A tool actuated vacuum automatically runs when the sander runs, and turns off when you turn off the sander. In fact it continues to run for a little while after the sander is shut down to make sure dust is cleared from the line. Uneeda’s vac is capable of doing this with electric AND with pneumatic sanders.
The sanders
For this video we worked with Uneeda’s Ekasand 3” x 4” rectangular and 5” diameter random orbit sanders. Both sanders use hook and loop sandpaper and provide variable speed. Hook and loop makes it incredibly easy to progress through grits by simplifying paper changes. Variable speeds is very valuable when you want good control, for instance when sanding a veneered material.
Conform to the surface
Complex profiles like molding or raised panels can be very difficult to sand. The sponge-like pad available for the sanders makes it easy to get the sandpaper to wrap and conform to the surface.
Sanding finished surfaces
It isn’t uncommon to need to slightly abrade finished surfaces before the next coat of finish goes on. This is another great application for the sponge-like pads, and also a great time to reduce the speed of the sander so you don’t take too much off. The Ekasand 3” x 4” and the 5” disc work really well for this.
More info
Visit the company’s website or call (845) 426-2800 for more information on Uneeda products.
Sanding is, unfortunately, I guess, a necessary evil that we all have to deal with and anything that I can do in order to make sanding come out better, go easier, and keep my environment cleaner I am gonna go after. So that's what I'm looking at here today is a sander setup from Uneeda that makes profile sanding and some other sanding we're gonna look at just go a whole lot better. A couple of things are happening here. One, tool actuated vac. So what that means is that when the sander comes on, the vac comes on.
When I stop the sander, the vac will continue to cycle for a little bit to clear the line and it's got great filtration on it. So I know the environments are staying clear. Now what's a real big deal with that is that even if you're not reacting today to sawdust or other products in your shop, that doesn't mean you won't over time. It has a, sawdust has a cumulative effect, cumulative negative effect, which can be that allergies can develop over time. So I harp on this a lot in my woodworking classes, you really want to make sure you're keeping your environment clean so that your lungs are protected and you can enjoy woodworking for a really, really, really long time.
Now, part of that is turn this electric tool on, the vacuum runs. With this unit it also has pneumatic capabilities and you may see the pneumatic hose that's also here. So in this case, if I had a pneumatic tool connected to this line, the vacuum will run with that pneumatic tool as well, same deal. Now in the world and making my sanding easier one of the things I really like is variable speed that gives me control so that I can make sure I'm taking off just the amount of material I want. Variable speed combined with proper grit selection goes a long way toward making sure you get the exact result you want.
And we're gonna see a huge benefit of that variable speed in just a little bit. I've got some beautiful pieces of molding here, and a thing to remember with moldings or with work that you do with a router is that those tools are going to leave mill marks. And if you put a finish on without removing those mill marks, it just accentuates them. So imagine a routed profile or a raised panel door and if we don't take care of this stuff ahead of time, it's really gonna pop. It's going to look bad when you get finish on.
So what we wanna be able to do here is use the sander to get down in here and flex into that profile so that we can take care of those mill marks. And again, imagine the profile on a raised panel door, not dissimilar from what we have here and the way that we could take care of that. Random orbit sander. So that motion is gonna do a great job of leaving us without any sanding marks in our work. Looking like this as we put it to work.
And then similarly some quarter round. And if we only had touch-o-vision, you'd be able to tell like I can that already, just in that little bit of work, what a significant difference from there where it's been sanded to here, it's very easy to feel the texture, the profile difference between these two parts. Now, in a similar vein, we put finish on something like a door, and when you're abrading finish between coats, we wanna make sure that we can take care of that. So for this, a sponge is, again, gonna be the answer for us. So we'll take this one off.
And just switch to a different product. On this door I've got a quarter inch radius on it, a quarter inch round over and so, like our trim, what this'll let me do is flex over that radius so that one, I'm not taking too much off of it, too much material, too much finish. And two, of course, I don't wanna change that profile. Now, this is a spot where, if you want to slow the sander down, that's gonna help make sure that the few mils of finish we have on there don't get knocked off and we end up back at raw wood. So I'm slowing her down a little.
That's leaving that nice and smooth, ready for the next coat to go on. Then on a large flat surface like this we would incorporate this random orbit sander, five inch disk, with, again, that same type of pad on it so that we're smoothing out our finish. We're not looking to sand wood at that point. We just wanna use that finishing pad in order to knock this down, get it ready for its final coat. But what I really wanna show you with this is pretty unique project I've got going in the shop here, and a project that really calls for good dust collection, a good sander, good control, and the right abrasive.
Oh, that's better already. This canoe is a labor of love of mine. I've been working on it for a while and where it's at right now is three coats of epoxy. It's got one more coat to go. Prior to that fourth coat going on, all these little high spots have to get knocked down.
So, I mentioned earlier, I see variable speed as a huge benefit. This is a spot for it because what I need to do here is make sure I sand the epoxy but I don't go through the epoxy to the fiberglass cloth that was the first thing that got laid on here three layers ago. So, if I get overly aggressive with sanding, then I'm gonna have to do a lot of do-overs here in order to catch up. So, again, great dust collection is important because I'm sanding epoxy. Making sure that I have good control, variable speed.
Making sure that I have a good quality sander so that when this is all done, I'm not leaving it full of scratch marks that I'm gonna have to deal with later. All comes down to the sander I'm using here in order to do the work. So, overall, in the world of sanding, none of us wanna spend anymore time doing that than we have to, so good sanders, good vacs to do the work. And one of the things that'll do is expedite the process, two, it's gonna make it easier so that you don't hate it as much. And additionally, when we get good quality from that sanding operation, whether it's raw wood or something that's got finish on it 'cause you're getting ready to do another coat of finish, when we're doing that with good tools, it's all gonna be reflected in the quality of the final product that we get out of that.
So, great system here in order to make all of that come together and make sanding go as well and as easily as it possibly can.
<strong>Ticket 38203</strong> Goof sandpaper's not cheap. I buy them in standard sheets and cut them to 1/3 size. In order for the sander vacuum to pick up more dust, you are using fenestrated paper. I noticed that you were careful not to go over sharp edges. I would think that the paper would snag when sanding on corners/edges and rip, a reason I've avoided them. I used to use a Black and Decker "Mighty Mouse" sander that looks like a clothing iron. It had Velcro-type fasteners and I found that the sandpaper would move (the fasteners not holding all that well) and the sandpaper would also wear out much faster than the best 3M sandpapers. I've often gotten what appears to be a nice, smooth surface, which stains beautifully but only later, when spraying on the final coats of varnish, do small sanding swirls in the wood show up. When that surface was a veneer, re-sanding it back down to what's left of "bare wood" can be treacherous but there are not a lot of options. What's your experience with these problems and with these different sandpaper types?
<strong>Ticket 38202</strong> Where do you get tool acuated vacuums
That canoe is exquisite! Well done.
Where did you buy that nice T shirt. It looks as good as all your woodworking projects.