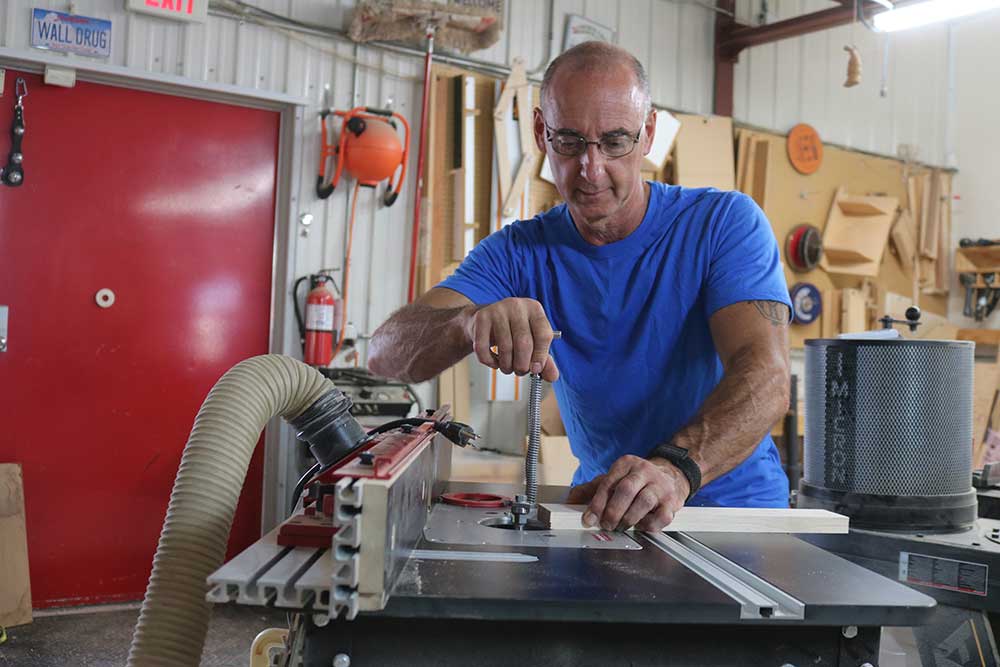
Kreg: Add Storage to Your Workbench
George VondriskaDescription
This project adds A LOT of storage to your workbench. We’ll do this by building a cabinet and slipping it into the steel frame. The project, and the companion plan, was designed for Kreg’s 32” x 48” Universal Bench. Adapt the dimensions as needed for other workbenches. Be sure to download the PDF plan.
What it provides
You’re going to love the massive amount of additional storage the cabinet provides. Four pull out trays on full extension slides, a flip up shelf for extra horizontal workspace, easy access pencil and glue brush storage and an end cabinet that’ll work great for glue bottles and finish.
Material
The cabinet is made from MDF specifically for its weight. Thanks to MDF the cabinet adds about 150 pounds to the bench. Heavy workbenches are a good thing.
More info
For more information on Kreg products visit their website or call (888) 447-8638
Having a good workbench in your shop is a must have thing and work benches in this style with a wooden top. The steel base are very versatile. They're easy to put together. They're gonna give you a lot of options. You can get the top with holes or without holes.
First step is to get your bench assembled. Assembling these benches is easy, just read the directions. One of the things that's key is put the bolts in, put the nuts on, but don't snug them until you've done this squaring step. It's important that these frames go together with the parts perpendicular to each other at that point. It's pretty much rinse and repeat.
I do like using an impact driver instead of a wrench or a ratchet to put everything together. It makes it go so much faster. And there are many, many nuts and bolts on these benches connect the ends to each other with a couple of long rails and then go through the same process. Use a square, make sure everything is right before you snug it up with the impact driver. Once the base is put together, slide it out of the way and bring in the top, center, the frame on the hardwood top and then drive screws to hold them together.
I'm a big fan of having everything in my shop mobile. If you are too, you can add casters. Otherwise you can just leave the leveling feed on the workbench and your workbench is ready to go to work. The benches are great. Except for one thing when you look under here, we're storing a bunch of air under there.
Wouldn't it be nice? If instead of storing air, we could store stuff we need in our shop like this, bam. Isn't that a cool cabinet? You can add this to your workbench. Now, if you're working with something besides this Craig bench, you're gonna wanna double check the dimensions and make sure the parts play nice with your workbench.
Here's what's going on. A lot of cool stuff inside here, pull out trays and full extension slides on that end. If this isn't quite enough real estate for, you can get a little bit more real estate from that flip up tray on this end. Another cabinet, it's just the right size for glue bottles, aerosol cans, little stuff like that. And on the front looking for a spot to make sure you can keep track of your pencils or glue brushes.
Anything that's like needs to be close at hand, it can go in those PV C pipes right there. This is a great addition for a couple of reasons. One, it gives you a boatload of storage under the bench two that's made out of MD F and that adds a lot of weight to the workbench, heavy workbenches or good workbenches. Let's have a look at material selection and why MD F I went with MD F medium density fiberboard for a very specific reason, it's really, really heavy and I had just mentioned that weight with workbenches is good. So of course, you can use any material that you want.
But as we build this out and you have a look at it, everything here, the doors, the drawers, the flip up, everything is made out of MD F. It adds, I'm guessing about 100 and £50 to the bench without any tools in here, MD F stays really, really flat. That's another good benefit to it. And if you want to paint this, when it's done, you can because MD F paints great couple things here. One is, there's a plan included with this.
You want to look at the plan and you're gonna get all the park dimensions from there. I've already mentioned if you're working with a different bench, you're gonna want to double check those dimensions and adapt them as needed to make them play nice with your workbench. First step is gonna be to process MD F and move those heavy sheets around. So let's have a look at bucking them down to rough cut size and getting parts finalized in size so that we can start putting bench parts together. Three quarter inch MD F is heavy stuff.
It's about £100 of sheet. So it's a pain in the butt to move around. But when you want to add weight to a project like I do on this workbench, that density, that weight makes it a good candidate. It's also a great paint grade material. It stays flat and it runs a pretty true three quarter inch thickness.
The best way to deal with it for your projects is to set it up on saw horses with sacrificial cut rails underneath it and use a track saw to buck your pieces down to rough size. I start by laying out parts that are oversized. All these big old slabs are gonna get cut to their final size in the next step, making two sets of lines makes the layout lines and the subsequent cuts parallel to the end of the sheet position your track on your two layout lines. And when it's in the right spot, fire up your tracks on and make your cuts. The next step on these oversized slabs is getting one and cut square to an edge, which is what I'm doing here.
Once you've got that cut made, be sure that you mark it so you can keep track of it as you're cutting these down to the final sizes you need for your project. Check the project plan, lots of these cabinet parts get pairs of pocket holes put in them. This really simplifies attaching the face frame and a little bit further along in the project pocket holes will also be used for our face frame joiners before we put anything together. Let's look at the finished cabinet and you can also be looking at your plan to get an idea of how all these parts play nice together. So one of the things we can see here is that the style on the right and the style on the left are the same width as it sits in the cabinet.
But when you look at the plan, you'll see that the style on the left is extra wide because what happens is the cabinet goes in and then it gets pushed over. So part of that style is buried behind that metal leg. The reason I'm bringing this up is when we go to put the cabinet together, you'll see that the mid wall behind this style is not centered on the MD F case. It's centered on the opening in the face frame. So you really want to pay attention to getting that right.
Otherwise it's gonna mess up your trade dimensions inside here. Now, you've got your parts cut to size. Wouldn't it be a shame if we had this whole box put together and it didn't fit in there? So I strongly, strongly, strongly recommend you do a double check on your parts before you start putting the box together. So one double check is grab the top or the bottom and you can have made this cut in scrap first and then bring the scrap here.
We wanna make sure that these pieces are fitting between the vertical legs. Now think about what's gonna happen with our mid wall and our two sides, we're gonna have a bottom and a top and those components have to fit vertically in between them. So the double check there is do that and then do this and then grab one of these and it better do that. It's got to clear those rails and I'm actually oh, a good 16th of an inch under that. I wanna make sure I have plenty of space to slide that cabinet in once the box is put together.
So do that double check before you assemble. Once you know that's gonna fly, we can put this baby together, assembly. Let's keep a couple of things in mind. We want to glue the joints, we're gonna brad the joints and we're gonna screw the joints. So don't get tricked into an idea of, well, MD F isn't that hard.
I can probably just drive screws without pre drilling. That's gonna be a really bad move because you're gonna split the MD F. You definitely wanna pre drill and counter sync before you drive any screws. General rule. The screw should be twice as long as what you're going through.
So three quarter inch MD F means I've got an inch and a half screw to make sure I have enough reach into that next piece from there. It's just gonna be a lot of rinse and repeat. Um We're gonna get stuff put together and the process is gonna go over and over and over and over and over. Check your plan. You should have pocket holes in these top and bottom pieces and we want those pocket holes facing what will be the front of the cabinet when we're done on your mid wall.
I'm gonna remind you again, it's not centered on the case. It's centered on the face ray. Make sure you get that right. And then the mid wall also gets the pocket holes in there which a little further down the road are gonna make it so much easier to get the face frame out. So don't forget about those, the mid walls, top and bottom are all put together.
So now I'm throwing them back on same agenda, glue brads, pre drill screws and I'll keep going with this. But I, one of the things I wanna mention is with your squeeze out like we have right there. If you grab a glue scraper, you can and that's gonna clean it off. So the key to that is don't let it get real hard when it's rubbery. Like on the one I just put on, this is too soon because that's just gonna smear the one that I did a little bit ago, that's rubbery kind of like caulk and that'll cut right off of there.
So take care of that glue all around. I'm gonna get this back screwed on and put in the back on is the end up to this point of our case assembly. You gotta cap the case assembly with a face frame, putting the face frame together is real standard face frame stuff, Cut it to size. I've got pocket holes joining all of the components here. I wanna reiterate the style on that side is extra wide because it hides behind the leg.
Look in the plan. It's all gonna make sense. Now, glue, remember the whole pocket hole thing with these case pieces. This is when that pays off. So right here, we've got a snake bite, we've got double pocket holes.
And the reason for that is we can use this clamp now to come into one of these, get everything lined up, clamp it. Then remember we've got double pocket holes here so we can do the same thing with the mid wall. Got the same thing across the top of the cabinet and the ends here. We don't have the benefit of those pocket holes. So my lying in the sand on that is if it's a visible area, I don't want those double pocket holes.
So we'll just throw a clamp and these hands, I am going to finish clamping. I'm gonna drive the rest of the screws and let this glue dry. So we can go on to the next step with this before we do anything with the drawers or trays like they're making them. We've got to get some fillers installed here in the case on this side of the cabinet, we've got that really extra wide style. So that's gonna be a little bit different piece of MD F with blocks behind it.
In order to make up the difference, you'll see that installed in a second on the other side here, this is pretty standard stuff. We're gonna have solid wood fillers that make up the difference between the case and the edge of the face frame. You want custom cut those, you want plain them to fit to make sure that they are flush right there. So now we can get those fillers installed. There's a couple tricks along the way to get them installed just right.
I'm grabbing my rails and my spacers and I'm going in. So here's the deal. The easiest way to get drawer installation consistent is to use spacers when you put the rails in. So with these little glue on the ends here and we've got our pocket holes one on top of the spacers. There we go.
When you do yours, you're gonna wanna check the dimension on that spacer to make sure it leaves you flush right there. The bottom one doesn't need a spacer then kind of second verse, same as the first. Remember that you gotta carefully machine these so that they're flush out here. And for consistency, grab those same spacers, couple of staples, bottom one sits right on the bottom of the cabinet just like on the other side. And then the other thing that's gonna help your consistency is a block that actually marks out where the slide is gonna go on this rail.
Do that same thing to the other compartment. Once all the fillers are in, we can put hardware in. So an easy way to do this is to put this jig right on those pencil lines that we established earlier. Then the case component of the slide sits on top of that, even with the front of the face frame drive a screw couple more times. Yeah, down here on the bottom, I've got a one inch spacer right there.
So that slide simply sits on the one inch spacer and do the exact same thing on ma. Now with the hardware in, we can figure out just how big the drawers and trays gotta be once the slides are in. Now, we know how big the drawers actually have to be. This is critical getting this measurement right? Because if they end up just a little bit too big, they're not gonna go in the opening.
It's OK for them to be a tiny bit too small. So at this stage of the game, put the drawer component of the hardware. That's this part in measure in between them, whatever that measurement is, subtract another 16th of an inch because again, it's ok for the box to be a tiny bit too small, then build your drawers. So this is construction. You've already seen, we've got three quarter inch MD F making up the draw box, a front and a back butt joint with a brad and screws and glue holding that together and then quarter inch plywood making up the bottom.
Once you've got these built, the next thing we can do is go back to our jigs, slide these out and the drawer just rests on top of those jigs. I like to put a piece of waste on the front here. I wanna not let this component get past the front of the door. So if I do this, yeah, I can bring that forward. Listen right there where it hits, bring that out a little further so I can do another screw.
Yeah, bottom line, follow the instructions that come with that jig. I need to completely remove the drawer. There's room in there for to get a third screw in there. Once that third screw is in, we're gonna have that. You gotta love self closing drawer slides pretty cool.
One more thing on these bottom trays where you can't use the installation jig. All you need to do is calculate the distance from that component to the bottom of the drawer box. For me a half inch spacer. I just use half inch plywood was just right. So set that on the half inch plywood with that setting on the bench and then you can screw that in to the drawer box to make sure it's a nice and straight and parallel to the bottom of the box that takes care of yours.
Doors are pretty simple MD F slab, quarter inch round over to take that sharp edge off. The only thing that's a little, uh, you gotta work with it. Kind of a thing is with the spring loaded hinges. I like these hinges. They're gonna keep the door closed.
But on the installation side of things, they add a little bit of a wrinkle. I'm gonna help you over that. So first thing, use a layout gauge and mark out the overlay on the exterior of the door. So in my case, the door is 3/8 of an inch per side larger than the opening. So I used my layout tool in order to put a mark three eights, 3/8.
Then same thing here. This is the kind of critical one. This board is clamped on those 38 inch lines. What that lets me do is come here and on this side, I'm eyeballing the top of the door hitting that overlay line. Then here I'm going to squish these and take that spring out of them.
I'm gonna force them flat and then push it against the step. At the same time, I'm watching my layout line on the top so I come out squish them, push, make sure I'm still on that layout line on the top, hold that door down. And then in this case with a pine face frame, you don't have to pre drill. If you're in a hardwood, I would pre drill these, the flange on the face frame will accept, um, two screws per hinge. Don't put the second screw in until you get everything kind of uncombed, discombobulated here and check the doors just in case you have to make a tiny adjustment.
Once you know they're in the right spot, then drive the other screw boom. So what I'll do next is I'll lay this down, make sure the doors are right where they should be, get those other screws in there and then also add your pulse here on the front of the doors and that takes care of getting doors on the cabinet. Pretty exciting moment. This is ready to go in there. Now, you can play this a couple of ways.
I'm gonna do this by myself because I'm stupid. Um, this is very heavy. Wouldn't hurt to get another pair of hands at this stage of the game, but it's on these stools which are almost the same height as the bench. And I don't know, well, there'll be grunting involved and stuff, but, and I'm a kid, you know. So here's where we're at, um, when I did the other one by myself, it went really well, this one, it kind of went off the rails like Ozzy Osbourne.
So, um, Chris, I'm gonna, I'm gonna phone a friend and have Chris come in and help and, uh, I trust you implicitly to not squish my poor little manos back here on these other rails. But yeah, we just gotta work it forward and in there like that. Now, a couple things, if this is really, really hard to do, which this just was the easiest solution is take off the doors and take out the trays and you'd probably lose about £80 just like that. Um And of course, another pair of hands is a great, great way to go right from the start. These rails have holes in them.
So what you wanna do now is crawl under the bench and drive screws through the hole in the rail into the bottom of the cabinet so that it stays in that position. So thank you Chris for saving my bacon. And, uh, I'm gonna get those screws in the rails and then we just have a couple more steps to go here. Let's gain some more storage space because the cabinet was pushed over and it's hidden behind those far legs. There's a gap there.
So I built a little end cabinet, took the doors off to make it easier to install the build on. That is exactly like what we have already done. It's butt joints between MD F, top and MD F side and then, uh, pine face frame. One thing a little bit different. It's got adjustable shelf holes in it and it's got pocket holes so we can sneak that in there.
I got, it'd be nice if it stayed. It's a cool application of screw pockets. I think that is enough to keep it there. I'll add the other screws in a little bit. The other thing you want to do here is make yourself an adjustable shelf that can then sit on pins in there.
So I'll come back, I'll drive the rest of those screws. I'll hang the doors. Now, look at this. We got another little space. That's where these are gonna live.
That's just PV C pipe from a home center, cut it 45 degrees. The other thing I did is I drilled a hole with a counter sink in it. So this is gonna be pretty simple. The 45 degree against that vertical face come up till it hits the rail and then we want a flat head screw for this. So we can see in that counter sink and then there and I did four of these.
You can do as many or as few as you want, you could fill that whole pile with those if you want to. Now, on the far end, if you want more room to work, we can add the flip up over here with any flip up shelf hardware. The thing you got to really work on be careful about is getting it installed so that the two arms are parallel to each other. If these end up, like if one's cocked this way and the other's cocked the other way, um, they're gonna have a really hard time operating. So the easiest thing to do is remember when the bench got put together a square was used to square off all these components.
So just let that sit against the leg and use the leg as a registration point to make sure that's straight up and down. And I am so dominantly right handed, I got a switch. So up against that rail, reading off the vertical rail and then with the shelf component just set that on there, center it, center it and then two with these arms, you wanna make sure that you're parallel now to the edge of this same thing. If they rack, then it's gonna make it difficult for this thing to go up and down. So I'm looking at the arm and the edge and there's room for more screws, but don't do that yet.
Make sure it's gonna work. If you've got stuff Klu in there, if it's Kittywompus, it's not gonna fold down, the metal parts will hit each other. So the reason for being minimalistic on screws when you're first getting this installed is if you need to, you could take a screw out move that, adjust it just a little bit, use a different screw hole and get that in the right spot so that it does what it's supposed to do. So this is showing me that's ready for me to put the rest of the screws in. In fact, that's done.
The cabinet's done, the drawers are done. This whole thing is done. What I really love about this project is the incredible amount of storage that we gain. And remember I said when we started, we're storing air, now we're no longer storing air, we're storing tools. So it's a great bench to start with.
And this makes it even greater now that we can use all of the space we have under the bench.
Would like to know your thoughts on why the Kreg track saw was producing sawdust not captured by the dust collection?