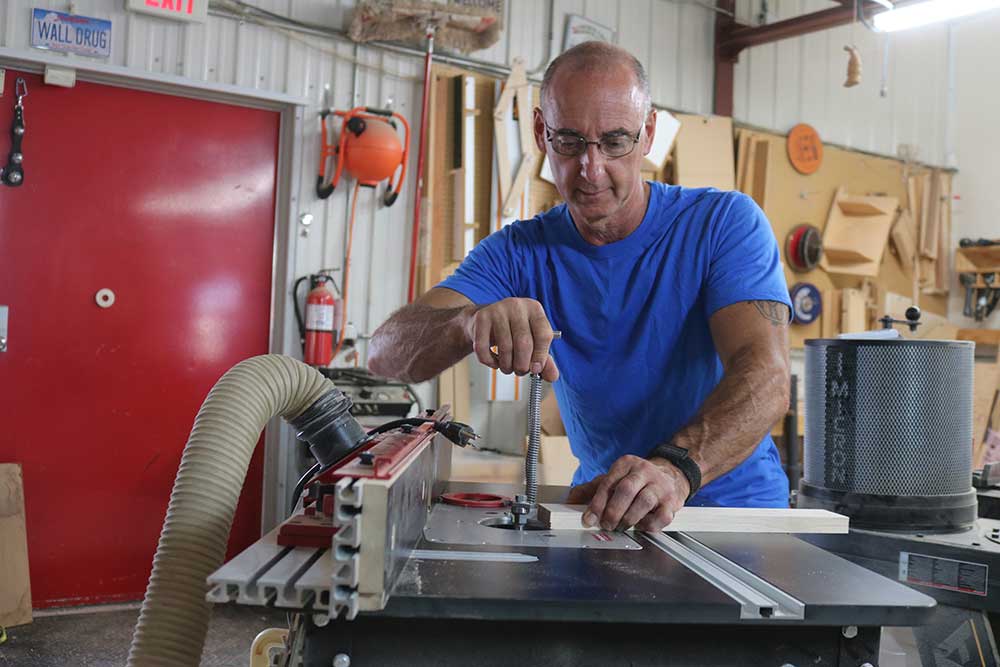
Using a Lathe Drill Chuck
George VondriskaDescription
What do I need?
The first thing you need is a little information. You’ll need to know if your lathe has a #1, #2 or #3 taper in the headstock and tailstock. Check your owner’s manual. A #2 taper is very common. If that’s what you have, order yourself a drill chuck with a #2 taper. Otherwise order a drill chuck with a #1 taper, or drill chuck with a #3 taper. It should fit into both your headstock and tailstock.
And then…
And then the door is open to use the chuck for lots of different things. When it’s in the tailstock use it to hold drill bits for boring out lidded boxes, or drilling tang holes in the ends of tool handles. Mounted in the headstock you can use it to hold pen mandrels, buffing wheels or a flutter sander. It can even serve as a chuck for small-scale turnings.
More about lathes
A wood lathe is a unique tool. Unlike other tools the wood is moving (spinning) and we bring the tool to the material. It’s very important to make sure you fully understand lathe safety.
You should also do a handful of routine maintenance items to and for your lathe. Maintaining your lathe isn’t hard. It’s simple stuff.
But wait, there’s more
If you want to make certain you’re getting the most out of your shop time, we’re here to help by providing more helpful shop tips.
Some very nice instruction. Allow me to add: When buying a drill chuck for the lathe, try to get one that is threaded to accept a drawbar. You don't want the chuck to vibrate out of the Morse taper at an inopportune time. Really bad things can happen. A drawbar will make sure the drill chuck stays put.
I would really love to do this as a substitute for using a very inaccurate hand drill. I have an old AMT lathe. Its tail stock clamps onto two 3/4" tubes that functions as its rails. There is some wobble at the tail stock until it is clamped down, but it still has a tendency to move away from the head stock as I turn the piece no matter how tight I make it. Before you say that I should go out and buy a new $2000 wood lathe, I also have a new Chinese metal mini-lathe and it has the same problems with head and tail stock alignment (even though it looks very much like your wood lathe) and lining it up to drill in the center of a brass rod is strictly via eye-balling. In addition, once you remove the tail stock from the turned piece in the wood lathe, it will no longer be supported on that end, so it will move and the center of the piece to be drilled will not be the same as the center of rotation. I even noticed that your piece was wobbling in the lathe as you drilled it with the forstner! I therefore have no confidence that a drill bit would be exactly in the center of the turned piece or that it would drill straight in-line for anything more than a short distance. A small drill bit would likely snap off. This would be even more difficult with drilling holes into long pieces, like furniture legs, which are too long to fit in a typical drill press and would only be supported in the head stock chuck. It's just not possible to drill a perfectly placed straight hole! Your method should work in theory but here are the problems: As you turn a piece, you are apply force 90 degrees to the head and tail stock. It's not just radial force, it is lateral force. That means that the turned piece will try to move away from the live center in the tail stock. You can tighten up the tail stock to compensate as you turn it but the hole from the tail stock still gets larger. As there is some lateral force against the head stock, when the tail stock is removed, the turned piece will shift and could even fly off of the head stock when you power up the lathe if you are not careful or if the turned piece is long. And then there is the problem with alignment between the head and tail stocks. They need to be exactly in the same line. Just touching the center it not good enough if its at an angle.
George, one of the problems I've had with using M2 tappers is getting some kind of dirt that scores up the faces. This makes it hard to get the attachments out. I bought a #2 reamer to clean the surface of the ID and emery cloth to the clean the OD of the insert. I try and remeber to clean the inside before inserting the tool and usually try and pass a paper towel through. Is there something you do to avoid this problem?