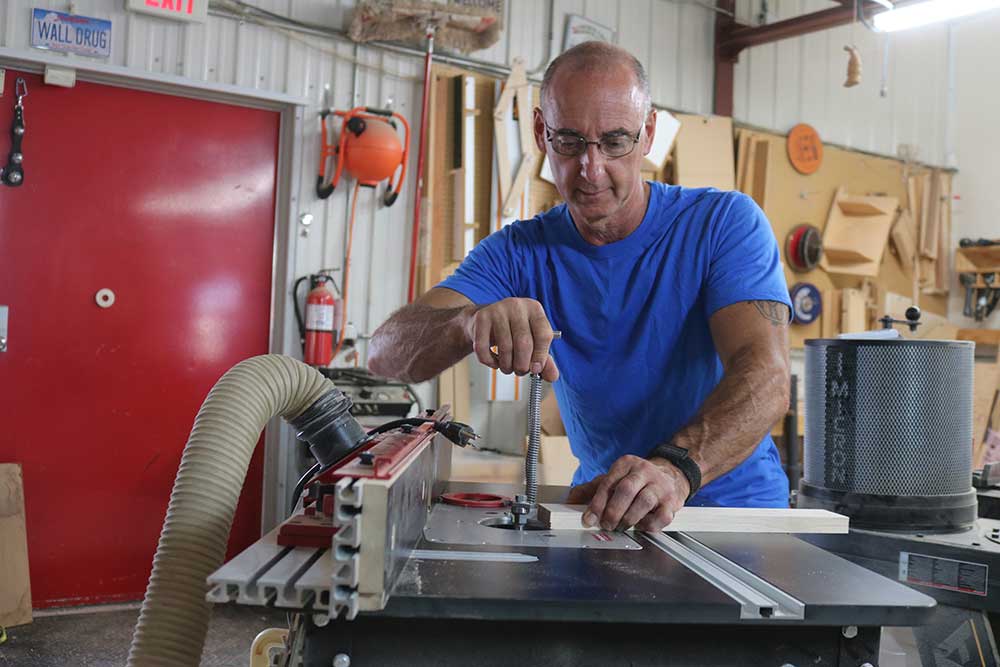
Make a Raised Panel Door
George VondriskaYou can easily create beautiful raised panel doors with the right setup and the right router bits. This video will guide you, step by step, through the door making process. George is using Freud’s Adjustable Rail and Stile set, Ogee Raised Panel Bit with Back Cutter and Roman Ogee bit. Freud’s Quadra Cut technology makes for smooooooth cuts.
Label your parts
It’s very important to keep track of your parts when making doors. This is especially important when you’re making a lot of doors. It can be very easy to get parts mixed up, or to mistakenly flip a piece over.
Coping skills come first
The first step is coping the end grain of the rails. It’s best to do this while the edges are still square. That makes it easy to support the outfeed side so you don’t get chipping when the cutters exit.
Then it’s long grain cuts
After the rail ends are coped you can do the long grain cuts. This creates the edge profile and provides the groove the panel fits into.
Making a panel
After the door frame parts have been cut, dry fit the door and measure for the panel. Install the panel raising router bit (and lower the rpm of your router) and you’ll be set for making raised panels. Do this in two or three passes. Get a router bit speed chart here.
Test cuts are important
Make sure you do test cuts before machining any of your door parts to double check the height of the cutters. This is also a good time to get a feel for routing these pieces.
Shape the edge
Glue the door together and add a decorative profile to the edge. An ogee was used on the rail, stile and panel, so was also used for the edge.
More info
For more info on Freud Tools products visit the company’s website.
Let's make a raised panel door. This work has to be done on a router table, and you gotta have a good set of router bits in order to do this. I'm gonna be using Freud bits. We've got a handful of different things going on here. This is Freud's adjustable rail and style set, panel razor with a back cutter.
I love these cutters and their OG bit and we'll use that to put a nice profile on the outside of the door when it's done. One of the things to notice is the quadra cut action going on with these cutters that is seen here on this cutter, and the quadra cut gives you so much better surface finish. There's one of the places that pays off so well on a raised panel because you don't wanna have to do any more sanding on that profile than you absolutely have to. So surface finish, great surface finish is a wonderful thing. Now let's get going on this with step one.
Prep your door parts. And once you have them in your hot little hands, what I want you to do is label them. With an ax on the back face. And we're doing an X on the back face because all the cuts we're gonna do here are good face down, so to make sure we're machining the parts correctly, the X should always be facing you. Next thing I'm gonna do is put cutter number one in, not telling you yet what it is.
I'll explain cutter number one once it's in the router table and we're ready for a test cut. Bit number one is in the router table. Bit number one for me is the ingrain cutter, the cope cutter, whatever you wanna call it, it's the bit that puts the tongue. On the ends of your rails, the rails are the horizontal component. Now, the distinct reason I do it first is that when our pieces still look like this.
We can do that and grain cut and because this edge is still square it's very easy to support it to minimize any chipping on the exit side. If we've already shaped this long edge. And we have to support that it's way more complicated where we're going here is we are gonna make a copen style joint that looks like this. What's great about this is that we've coped the end grain that's the cut we're about to make to perfectly match the long grain gives us really good glue surface here, makes for a very, very robust corner. When you get the cutter in the table, set the height of the bit so that on the resulting piece we have a lip on the bottom.
And a shoulder on the back, the proportion between those two is about 2 to This shoulder on the back about twice as deep as the lip on the front is thick. Once you've got that set, do some test cuts, make sure it's right. The next thing we need to do is get the fence in just the right spot. This is very easy. There's a ball bearing inside the cutter.
The face of the fence is made error is made even. With the face of the ball bearing, so I do that by just bridging the opening in the fence that's obviously way too far back come forward until that levels out. And you're ready for your end grain cut. Couple more things going on. We can't just grab our rails and do this, wouldn't be safe.
plus we have, we haven't done anything to help on chipping on the exit side. So what we're gonna do is take a piece of scrap, put that against the fence, rail against the scrap, make a cut. Big deal out of this is you took the time to label your parts. Make sure you can see an ax all the time. We wanna cut, rotate, cut, not cut flip cut.
Ease of feed is real good here. Cut quality on that end grain cut is great. Next thing we're gonna do is swap bits to the other door making bit and then I'll show you how to get the height on that correctly set so we can do our long grain cuts. Next thing, install your long grain cutter for height on this bit. The easy trick is grab one of your rails where we've already got the tongue produced, where this has a tongue, this has to make a groove, so do this.
And this and when that carbide is even with the top of that tongue, you're ready for a test cut. When you do your test cut, what we're looking for the test is when these slip together. The faces need to be even. That's what controlling the height of the long grain cutter will do is either put a step in this or result in them being flush. For fence position, we're gonna do the same thing all over again, which is take advantage of that bearing, bring the fence forward.
Till the face of the fence and the bearing are even. I'll get my guard in place, my feather boards in place, and we'll be ready for long grain cuts on all four parts of your door. When you're ready to go on these longering cuts, remember again X marks the spot, meaning the spot you can see it's especially important on these rails we're committed. We have to make sure we keep the same face up. Got that great cut quality on that OG profile that we're using here.
Next step for you is dry assemble the frame. Measure it and that's gonna tell you how big the panel has to be. We need to get the panel cut to size and we'll be ready to raise a little panel. Next step, put in the lovely panel razor. These panel razors with quadracut and back cutter are an amazing router, but make sure you lower the RPM on your router.
Large diameter, low RPM. To get the height of this approximated, grab one of your door parts. And slip a quarter inch something into the door and then when we do this. We want this to end up in between those two cutters. Once we're close, then the next step is to do a test cut with your test cut, I did mine.
And that piece of poplar. Once you've got that, what we're looking for is when we put this together. Does the top of the panel line up with the top of the frame? And as you adjust the panel razor up and down, you're gonna change that relationship ending up with these flush is a benefit because then if you own a drum sander once the whole door is put together, you can send it through the drum sander to clean everything up. Now, what we wanna do is do this in multiple passes.
So I'm coming ahead of where my final pass will be. And the same rule applies to our panel. That's one of the things that's great about this cutter set is the consistency of it, which is everything gets fed good face down. So when I examine my panel, I want to mark the back face and make sure that that stays up for all of our cuts. Uh Now if you were watching with feel or vision, if there was such a thing and you were able to do that like I am, what great cut quality in this pretty porous red oak across the end grain thanks to that quadra cut cutter.
Next step glue the door together. And then we're gonna meet back here at the router table for a nice detail on the edge of the door. Very nice OG detailer on the outside of the door which matches the detail on the inside of the door because the Copen style set is OG, the panel razor is OG, and again, you know, especially when you look across here across that end grain cut quality. Out of that quadra cutter OG cutter is really, really good. So with making race panels, this is a methodical thing.
Take your time, label your parts, do test cuts, but it's not difficult to do and with a good set of cutters you're gonna end up with a beautiful race panel door.
Share tips, start a discussion or ask other students a question. If you have a question for the instructor, please click here.
Already a member? Sign in
No Responses to “Make a Raised Panel Door”