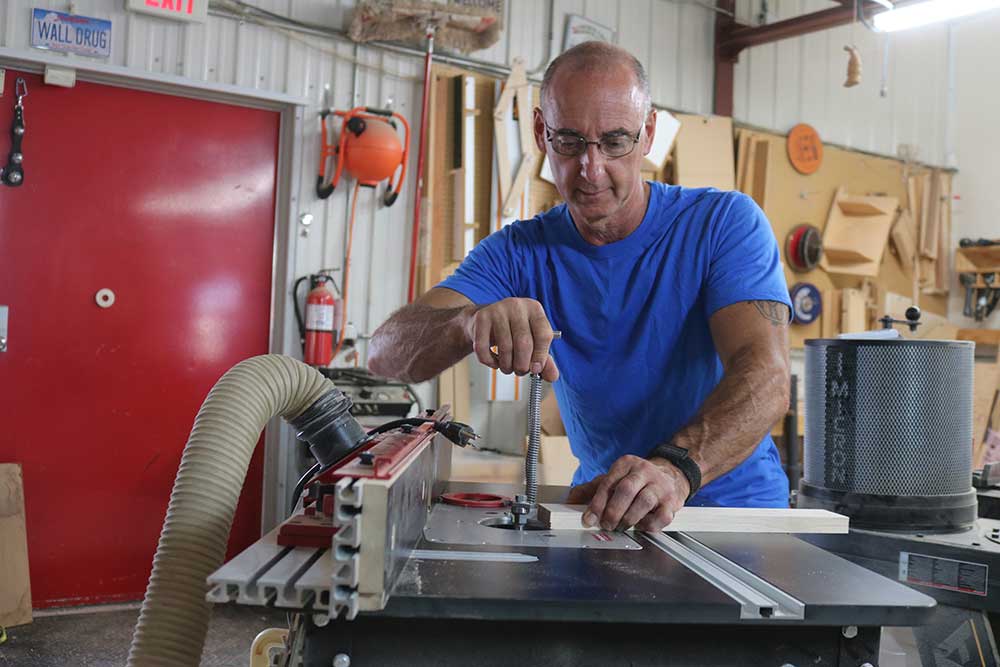
WWGOA Cutting Board Challenge 2023
George VondriskaDescription
Additionally, we’ve put together a collection of how-to videos, guiding you through the process of making various cutting boards, including end grain designs and crafting juice grooves. Make sure to sign up for access to the free videos and plans.
Follow Elisha Albretsen as Pneumaticaddict on Instagram and YouTube, or visit her website.
Follow Char Miller-King as Woodenmaven on Instagram and YouTube, or visit her website.
Follow Paul Mayer as Toolmetrix on Instagram and YouTube.
.
Hey, folks, this is a very special live presentation and I have to say this has been many, many months in the making. This is very cool. This live is not just me. Um But also at least if I'm pointing to my screen, we've got Paul Alicia and Shar with us as well. And here's what happened a bunch of months ago, we started looking for a project that we could throw out for.
Um, people work with WWGO A to work on while at the same time providing you with some cool stuff that you could do in your own shop and knowing that um the holidays are right around the corner and just in general cutting boards make great gifts. We landed on cutting boards. So, you know, like not literally because we didn't like jump off a table and land on cutting boards, but we decided we decided about, we decided we would do cutting boards. So, um yeah, so if you could see people, they're all kind of, you know, hashtag dad jokes. Um So in the end, what happened is um Shar, Paul Alicia and myself all made a cutting board.
That's what we're here to talk about today. And then we've also created this huge hub of cutting board activity. And there are links to that in the description for where you are right now. And when you go to that hub, you can get a PDF that includes the directions for each of the cutting boards. We are about to show you.
And then on top of that, there are five different how to videos related to cutting boards. I'm gonna talk more about those videos as we get a little bit further along. So, um we really want to keep this with your questions. We really want to keep this cutting board specific and um stick to that topic for the next 50 minutes or so. So, what we're gonna do is each of the um cutting board creators is gonna talk about their board and what they did to make it and a little bit of the background with it and then we'll go through that rotation and um I don't go on from there.
So you're welcome to post your questions as we go and then I'll grab them and I'll get the questions in front of everybody who's here on the cutting board board and then uh we'll see what happens. So, Paul, you are first, sir. What you got, dude? Sounds great. Thank you, George.
So, yeah, so the cutting board that I decided to put together for this was very simple in the world of cutting boards. So particularly if I compare it to the one that Alicia made and the one that shar made and the one that you made George, uh, those are, you know, much fancier. So this is a very basic end grain cutting board. I love making end grain cutting boards because they just, they, they work so well and they're so durable over the years. I have one that's my daily user that's about 12 years old and I put a fresh coat oil on it every once in a while and it literally looks brand new.
So a couple of kind of, I I'll, I'll share five kind of observations, I guess. First, just an overview of the cutting board. What is a little bit unique about this? And it was kind of an experiment was I had a piece of uh sap wood. So if you look at, if you look at first at the, at the first photo that, that I provided, uh that gives you an idea of what I attempted here and this was to give the appearance of an inlay.
So th that diamond shape kind of looks like an inlay, the repeating uh sequence of five diamonds running down the middle of the board. Actually, what that is is sap wood from the same board. This is all from one piece of cherry, black cherry and it had a strip of a sap wood running down one of the edges that my initial thought was I'm going to cut that off. So I'm working with all one color and then I decided it was kind of a triangle shape in the corner. So I decided, let me see if I can incorporate that in.
So as I cut it up into strips and glued it together, I put those in close proximity. And then as I went through the sequence of uh gluing it together, I alternated them and put them adjacent to one another so that you end up with that diamond pattern. It's very simple in execution. Uh And just I kind of experimented with some different ways that that could be laid out. So if you look at the second photo that I provided, you'll see the board that I started with.
And where I'm pointing is the sap wood. It's a little bit hard to tell on that uh on that piece. But that uh on the edge is the sap wood, which is much lighter on cherry than the heartwood, which is the darker portion. So I just left that in and created that diamond shaped pattern by putting four corners adjacent to one another to create that pattern. Now, a few things that I've really learned over the years in making cutting boards and I had a cutting board company for a number of years and have made many, many, many cutting boards.
So one on these end grain cutting boards don't be shy on glue. Uh you're gonna end up needing, especially the first couple of times you go through it, you're gonna, you're gonna use more glue than you think you should. But uh, glue is cheap. Uh, go ahead and overdo it and, uh, if you end up as you get experience and dial it back a little bit, that's fine. Uh The these end grain cutting boards, you're basically as the video and materials that George provided will show you you're making a cutting board then cutting it into pieces and gluing those back together.
So the tricky part about end grain is getting that second glue up. Uh Perfect. So what you want to do is when you're planning that first cutting board, run a, a leader board and a trailer board through your planar to eliminate the potential for snipe. Even if you think your planer doesn't snipe. This is, this is not the time to find out that it does because if it snipes just a little bit, it could cause a big problem with your cutting board.
So make sure that you're using that leader board and trailer board to lock the cutter heads and avoid the uh when you're finishing an end grain cutting board, get a huge bottle of mineral oil because those things drink mineral oil like you wouldn't believe it in the video that George shared. It shows letting it uh soak all the way through till you can actually see it coming out the bottom, then flip it over and apply it liberally on the other side. It feels crazy how much mineral oil you're going to put on there, but just give it all it'll take, don't hold back and that will make sure that you will not have to add a lot in maintaining the board. It will stay very good and, and repel water for a long time. Uh When you do that second glue up, be as meticulous as you can to get it as dead flat.
Every, every millimeter makes a huge, huge difference. So get that thing. So you can't even with your fingernails feel uh a catch because in your sanding step, you're gonna thank yourself if you did. If you did a really good job. Now, many of us don't have AAA dedicated uh drum sander.
The last tip that I'll share with you is to sand that quickly. Uh If you don't have, if you have a friend that has a drum sander, great. If you want to buy one great. But if you don't have a friend with a drum sander, you don't want to buy one. Take a spray bottle of water, get the top damp, let it soak for about five minutes to soften it up.
Then take your random orbital sander with about maybe an 80 grit. Uh And I timed it rips through it so quickly. I timed it one time. Let me check. It was three minutes and 46 seconds.
And that was on if I remember right, 18 inch by 18 inch thereabouts cutting board and, and that top was flat and ready for the next grit. So it's, it can be done very quickly if you take that spray bottle step. And that takes a lot of the intimidation and frustration out of end grain cutting boards because end grain can be slow to sand George back to you. So it, the, the style that Paul did here has become my new favorite style of ending cutting boards. And uh if you watch the video series, one of the videos is a spec specifically about making ending boards.
And it's one style is kind of the checkerboard style that we're all used to looking at. The other one is the style Paul did and it's a piece of elm that I used for that. And the, the book matched grain in that final glue up is just crazy cool and you just don't get that from a conventional end grain board. And honestly, it's simpler, start starting with one slab instead of doing multiple glue ups to end up with an end grain board. Um, lazy person that I am is way e look at Paul nodding his head um on a lazy statement.
Um It's a way easier way to execute this very, very cool board and a great use of a great job getting those diamonds together in the middle to really provide that pattern. All right, Alicia, you've got a very cool popsicle stick thing going. So tell the folks at home, uh, show them your board. That's, it's a cool board. Thank you.
Yeah, I, I guess I kind of came up with this. I was wanting to incorporate color into a cutting board. I had seen, I bet any, anybody who's a turner probably saw a few years ago those stabilized colorful blanks that people were using for pens or for, you know, knife handles and stuff. I think there's actual name like a brand name that, that makes the, the blanks. Anyways, I had been gifted a couple of different, you know, scoops and knives and things like that and I love that bright color.
Um, but when I did some research, I was looking into it and a lot of those bright colors aren't always food safe. So it's not gonna be recommended to be used for something like a cutting board. Um, and I looked around and I was at the craft store and I saw they have huge assortment of what they call craft sticks. They're popsicle sticks. They're, well, these ones are big ones.
So I guess there'd be tongue depressors. Um And I noticed that they were all food safe, you know, obviously, something that a kid is gonna put in their mouth needs to be food safe. And so that gave me the idea to start incorporating it into a cutting board design. So um the things that are important to keep in mind with the popsicle sticks are the fact that you have limited lengths, right? So you're just gonna be when you start this.
Um I started by gluing up little bundles and you can make whatever pattern of colors you want. I mean, they literally come in the rainbow. So whatever colors you, you know, designs, you could do red and green for that for Christmas, if that's your thing or blue and white for Hanukkah or whatever. Um But you basically, you're gonna want to start by creating these little bundles. So if we can take a look at the photos, we wanna see, there's the final look with the rainbow stripe in it and you could, you could laminate more if you wanted and you could go as white as you want as well.
This, I think I did two sticks of each color for this board. Um And then if we take a look at photo two where you see the glue up, so, um you're gonna wanna glue them up and something really important to keep in mind is you want to use a glue that it dries completely clear. That way you keep the intensity of color. You know, most wood glues as we know, kind of have a yellow or kind of amber tint to them. So you're gonna have to look around.
There are a few manufacturers that make a clear glue. I I've used. Dap. I know, um Tight Bond makes a clear wood glue as well, but you wanna be pretty generous with that. Make sure that you get good coverage as you're laminating together then.
Um Yeah, great. The photo is when you start to join your pieces together, the sticks are only seven inches long. So you're gonna be limited to your board being seven inches long or you're gonna have to figure out a way to join those little bundles together. So, with this project, I just did a simple miter joint, uh makes it pretty simple, not super distinguishable. But if you looked really, really closely, somebody might be able to see where that joint is if you wanna get fancy.
Um, you know, you could try doing some fancy coping and some scarf joint or something, but I'm a little lazy too. So I went with a miter joint. Um I also experimented by doing a finger joint. So cutting all of the ends of my popsicle sticks square and then creating a staggered finger joint type scene. Um And that seemed to work.
Ok. But honestly, the miter joint was less perceptible when it was finished to me than the finger joint was. So you get your strips all glued up and then it's just a simple of, uh it's the simple process of creating a face grain cutting board. You can rip down your side, you know, get a board that you like rip a strip off of it and then you're gonna insert your laminated strip. Luckily, this project is really easy to do a batch build of.
So, if you are making this for gifts, go get yourself a 6 ft board, glue up a whole those little bundles, you know, 6 ft worth of them, you know, join them together and then, uh, you can do one big glue up joining whatever your hard wood that you're using for the body of your board is with those little bundles of the colorful strips, get them all glued up together and then once everything is nice and dry, um, you can either plan it like that as one big board or if you want a little bit more control, you can chop them down into smaller segments and then run each one through your planner. Um And that's, yeah, that's pretty much it. It is a simple build. The only thing that's a little tricky is, it's a little fiddly working with those tiny popsicle sticks. Sometimes I have had some questions about the color Fastness and I think that depends on the brand that you use.
So I experimented with a couple different brands, the ones that I got, I actually found at Michael's craft stores. Um, they seem to be really good at being color fast. I, I scrubbed them several times with the soap and water kind of simulate what it would be like if you were actually gonna wash the cutting board and the color stayed true interest. Interestingly, I've noticed some of the colors are a little bit more color fast than others. So, um, you, you might have like the purple might fade a little bit more than the red.
But, uh, once you seal your board with a, an oil, which is what I recommend, um, it will really intensify those colors so that the scarf joint and I think you, you said you could do a scarf for, but I think you did, I mean that Miter that you created so that they overlay each other like that. That's a common way to put a board stretcher on a board and, and make short stuff, long stuff. Um Same on the cedar strip canoe, I'm working on. It's uh sometimes that's how you get 17 ft pieces of cedars by scarfing those ends just like that. Um And the other thing that's important for the people who are watching at home, especially if you picked into this came into this a little bit late.
Everything Paul is talking about Alicia and Shar and I are, all of these details are in a PDF. So when um Alicia is talking about the popsicle sticks that she got from Michael's, they are sourced in her, how to of the PDF along with the clear glue, along with whatever else, any stuff that got used. Um We've provided that for you so that you can make these cutting boards at home. Um, well, sure you are next. Are you ready to talk about your cool board that, you know, your bourbon board or no, your drunken bourbon board or there, there was some bourbon but after the board was already built.
All right. All right. Yeah. Sure. Um, I usually make pretty basic cutting boards because I'm teaching people how to use power tools and that's like the gateway, um, gateway to woodworking is a cutting board, but I wanted to do something different and unique for this challenge.
So I decided to go with the drunken cutting board and I can't tell you how many people said, did you really glue all those little pieces of wood together? So they couldn't figure out the process. So I have, I think we all have a bunch of scrap wood laying around or pieces that we just weren't sure what we were going to do with. Uh one of my favorite species of wood is wormy maple. Some people call it Ambrosia maple, but I just love it because every piece is just so unique and what the tree thinks is harmful.
We as what workers think is beautiful. So I had a couple pieces of that and just some Standard maple, some walnut, which is my second favorite. And Angelique wood, which is really hard and it's really hard on the table saw unless you have a really good rip blade on there. Um So I use a little bit of Angelique wood, little walnut and then add a couple of pieces of wing A we know that tends to be a little bit pricier. So I, I use a few pieces.
I made two separate cutting boards first. So there's a lot of glue ups happening here. So get your patients and your clamps and your glue ready because I think in the end there was a total of three separate glue ups. So I made the light board and I made the dark board. I glued those together.
The important thing here is to make sure that those boards are, are of even thickness because if they're not, then the end results, it's gonna multiply later on and it just won't be right. So after I glue those together, I didn't have any, um, woodworkers, double stick tape. So I just use some blue paint tape and fix it together with some C A glue, some Star Bond C A glue and a little bit of accelerator. Put those together. And then that's when we start.
Um, it's going a little fast, faster than I'm talking. But you guys see the end result right there of two different cutting boards with what did I say, four or five different species of woods. But as you can see right there in that photo, I am, um, just making random lines. Some people do it like every inch or every half, 1.5 inches. I didn't mind sort of random because sometimes we know the, uh, the band saw has a mind of its own.
I'm using a 38 inch, um, blade. I think it's, uh, three TPI, I believe, three or four TPI, I can't remember. Um, that's on the, the grizzly saw that I'm using there. So the most important thing that you have to remember when you are doing this project is to number all of your pieces because I assure you from that very first cut. If you do not mark that you will spend the rest of the evening trying to match those pieces back together, um You can go to the next photo, please.
So once I had the light in the dark glued up together, you basically end up with two separate cutting boards. So you're taking one from the top, one, from the bottom two, from the top two from the bottom and you're switching them and that's how I got the light dark. So that's um glue up number two right there that you're looking at to go to the next slide. So after glue up, number two, I turned the board horizontally and I actually did mark it here because I, I wanted to have a more even pattern as I was going. So I did an inch and a half of each time and I think I ended up with maybe 11 pieces after that can go to the next slide and then that is my final glue up and I, I think it came out great for my, my first, uh, drunken cutting board.
Uh One of the other problems that I ran into was Chatter Marks from the band saw. Those are almost impossible to remove. I initially tried it with, um, I have a surf prep, uh, standard that I used to try to get through the curves because if you mess up the curve, you'll end up with a gap. That's like the worst thing that happens during cutting board process, right is we have those gaps that um that just don't line up. So I also use the oscillating sander very, very carefully.
I think I had maybe 100 grit sandpaper on the sander to get rid of those chatter marks. And for the most part, it did what it needed to do. If I did this one again, I would start with probably uh eight quarter instead of six quarter because there is a lot of planing happening regardless if you, if you remove the glue before or not, we always get that little bit of glue that's stuck between the board and the clamps. But I ended up doing more planning than I wanted to. So I'll probably start with thicker, thicker wood the next time.
But it was, it was a great, it was a fun build. And um I'm so happy to, to share with you guys and I hope you guys go out there and try and make a drunken cutting boards yourself. It's, it's cool because I love how, um, well, like you said, when you started, people look at this and they think that you scroll, saw every one of those individual chessboard type pieces and then put them together or, you know, in my shop, see and see every one of those individual pieces and try to put them all together. But it's neat. It's like a lot of woodworking things where there's a secret behind the methodology that actually makes it way simpler than it looks when you look at the finished product.
And like you said, what a what a great use of all these because you start with a face grain glue up. So it's a great use of um all these individual strips we end up with laying around the shop all the time. But the key is to create the contrast, right? So having one board that's primarily darkish and one that's primarily lightish. Very cool.
All right. Um Well, Nick, go ahead and throw my photo one up there and I'm kinda, I wanted to be just like sha when I grow up. So I went in kind of a similar direction but not identical direction. So, um I've done this approach in bowls many, many, many times. And what I like about it is like shas drunken boarded.
When you look at this when it's done, it looks like you put this really complicated inlay into the project, but it's really simple to execute. So go ahead and jump to the next one. So the key to this is you do a, do an edge grain cutting board and then use a flexible curve to put a curve onto the board. Um So I'll give you a tip here. I I love, this is my newest approach on flexible curves which is squeezing them in between a one handed clamp, squeezing them in a one handed clamp to create the curve and you just squeeze more or squeeze less to get the curve you want.
And I've done it with strips of wood like I'm doing here and I've done it with um metal rulers as well um to get the curve. So once you get what you want, uh trace that onto the board, go ahead and hit the next one and then band saw that. So I'm doing this with a, a quarter inch, four tooth per inch blade. And my advice is practice, practice, practice, practice because you wanna get this to flow. You want the curve to flow as much as possible from one end to the other, which means you're trying to really make a continuous pass with no stops and starts along the way.
So um try this a couple times on scrap hardwood before you try it on your first board to try to get that curve as be a curve is possible right off the banda and then, um, make thin, thin, thin strips and glue them in. And, uh, it's just as simple as it sounds. As long as that strip, you made flexes to the curve, you can glue both sides of that joint. And then, um, when you close the clamps that's gonna force it in. And now I can't remember.
Do I have one more picture Nick or that? Yeah. So, um, squeeze this closed and then once that glue is dry, we'll go back to the bandsaw, cut the second curve and it's just the same thing all over again and then flatten that all on a planar or a drum sander and you end up with the Inlay strip when you're done. So another one that it looks more complex than it really is and you could do that edge grain or end grain. Um That approach in either style of those boards and you could go as far as you want with those inlay strips.
You know, if you wanna cut 50 of them in there, you could cut 50 of them in there. Um So before we jump on to a little bit of the, um the background videos that we did about the cutting cutting boards. Um Anything else from you three that, you know, now you've seen all the other boards. So any other kind of free flowing commentary here? I have a question for you, George it.
If you wanted to get a perfect radius. Could you set up a jig on your BSA or even something as simple as like pinning down the center and then you could just rotate your board and you get a perfect radius that way. Yeah. So a circle cutter would sure simplify introducing that arc and then you wouldn't have to worry about freehand flowing through that and uh and not having starting and stopping points. So, um it's a great idea because then you could just set on that circle pin and pivot, then it kind of has to come out.
Right. So, yeah, it's a good idea. I had a question on that arc as well. Uh I was wondering what, what band saw blade kind of with tooth count? Would, would you suggest to get a smooth for me on my, I did that with a quarter inch for tooth and then I, I do a different approach from Shar.
I, my goal is to not sand. Um Because I don't, you know, it's like Shar said with the surf prep sander, like if you distort, if you sand this curve a little more than this one, then you're gonna have weirdest. Um So, um, part of the blade selection is aggressive enough to go through inch and a quarter hardwood, but not so aggressive that it looks like I did it with a chainsaw. Um And then when you close that up, if it's so like in this case, that's a hard maple strip that's laid into the rest of the hard wood board. Um, there's a little bit of a flex there.
So, you know, if you have a little bit of a whoop de do that, inlay strip is so thin that it'll force into that, um, weird shape. Uh, a little to an extent. Um, if you do a big hook up and hook down, it's not gonna go into that, but if you have just a little bit of a distortion, it will do it. So, yeah, it's, um, same with bow blanks. Um, quarter inch four tooth has served me well on this approach.
So you didn't have any issues with chatter marks. Well, there's bands on Mars, you know, without question, but, um, that thin piece of maple almost acts like a gasket between them. And, um, I know that if I, if I cut and then I kind of reposition and I cut and I reposition and I cut, then there's gonna be jumps in that cut and that's gonna be bad. So that's where trying to free flow from one corner, cut, one continuous curve to the other corner is important. And that's Alicia's idea with the circle jig is a great idea.
Um, or you could do an Ellipse jig or no, I don't know if you can do an Ellipse jig on a bandana, but, um, you could certainly do a circle jig and take out that free end portion that would make it flow better, but it's, you know, even looking at this close, I'll send you a picture. Sure, you can zoom in on, um, that you can't see like tooth marks in between the strip and the, and the rest of the board. Impressive, dumb luck. But thanks. Well, let's look at, um, so again, for, for people at home who are watching, we've got this portion which is, um, uh, the cutting boards that Sha Paul and Alicia contributed.
We've got that in a PDF precisely how they made those boards that's all available, able to cutting boards in general. I put together five different how to videos and we'll give you just a little background there. So, you know what that's all about. So, um, one video, one video is just in general how to build a cutting board. And one of the things that we hit on there is covering, um, the best woods that you can use for a cutting board and there's lots of choices here.
Um, we wanna stick with hard woods. Um, but there are woods that are too hard and shouldn't get used. So the, um, Jena hardness scale figures into that. So we cover, prepping the material and, uh, how to make sure it's ready to go into a cutting board once you've got this material in hand, the next thing is to start composing the board and, uh, this is a fun step, but it takes a little bit of thought you want to pay attention to what you're doing here. Um And it's about contrasting colors.
It's about, for me, it's about also contrasting dimension so that we have a variety of sizes that we're working with here in order to get a end result. Um to detail the boards, there's a lot going on um radius, seeing radius, the the outside corners as well as the top and the bottom corners coming back and hitting those with the sander so that you've got everything nice and silky smooth. Um And probably most importantly, what's a good finish for this? We wanna be food safe. So, um, as an aspect of the video is we look at, um, we talk about different finishes that you could choose to use on your cutting boards.
And, um, oddly in us within us for, um, I think a couple of us use the same one and then a couple of us diverted just a little bit from that. So, um, that PDF will give you more choices and cutting board finishes as well. So then the, the just general how to make a cutting board is the starting point. Um Because you need one of those in order to make an ending board, you need an edge grain board to make an end grain board. So there's a separate stand alone video just on doing end grain boards and that starts with um cutting up your edge grain board and then reorienting the pieces.
So there's some flipping, there's some rotating and a cool aspect of this is if you work more than one board at a time, you can interchange pieces and get some really cool patterns going on. Um When you flip here is when you really start to see what it's gonna look like. And then in the glue up, this is what Paul was talking about too, with maintaining um, alignment on your parts. Um using these calls in order to make sure all of those little checkerboard pieces are gonna line up in. There is a really critical way to get this to work.
And then this other style of cutting board, this is that piece of Elm I was talking about. So this like Paul's, this started as just one big slab of Elm, which is then becoming an ending cutting board. So when these pieces get stood on end or yeah, on end like they are here. Um Every pair book matches, that's the pith of the log you can see right there. Um And in fact, as a piece of Elm, I cut on my sawmill, um probably 15 years ago or so, I think it's dry.
Um And the stupid thing is I've been moving it around for the last 15 years waiting for a project to use it for um with rain boards. Those should not go through your planar because your planer can catch that and kick out pieces in a very dangerous way. So one of the things we've got for you is a, uh, a leveling jig that you can make in your shop and a leveling jig. It, it, it's great for end grain boards. Um, but outside of ingrain boards, if you just one, if you don't own a planer or if you build a board or you're working with a slab or something bigger than your planer, this, um, this jig is a must have so that you can level stuff very, very easily.
And this is a way like Paul was talking about his trick of wetting the wood. Um You would do this before you start your sanding step to reduce the amount of sanding. You have to do, get a really good surface, finish off that router bit. Um And you're starting with something that's already dead flat. Um The other thing we know people like a lot is adding a juice groove to the board.
I I keep referencing cutting that big chunk of roast beef and the juice is flowing off of it. Um So the juice groove jig that we've got for you completely shot, made really easy to build, adaptable to any size cutting board that you want. And um it's, it's a very simple process which is the core box bit to work your rare rock, work your way around and multiple passes and add that juice groove. Um So that's uh another video we've got for you is how to make the jig and then how to use the jig. And then the other thing we considered is that, um, especially on big cutting boards.
It's nice if you have a way to pick them up big heavy cutting boards, besides, you know, trying to reach your hand underneath. So we've got a video that's all about cutting finger holes in the end of the board. So if you wanna do finger holds on your cutting board, we've got three different approaches here. It's all done on the router table. Um Three different approaches, three different router boots.
So with one of the approaches, you do end up with a distinct front and back on your board. With the other two approaches, you end up with cutting boards that can still be reversible when you're done because the hole that you see there is centered on the thickness of the board. So, um there's a lot going on here and it's when we call this, um, overall call this the cutting board hub. It's a great word for it because it really is lots and lots and lots of um information that's there to really help you go down the cutting board road. So I'm just, I'm scoping for questions.
Um What typically happens for me on these live streams is about 30 seconds after I say we're done, 10 questions come in. So, um, if you folks who are watching have questions, this is your opportunity we've got a little bit of time left to stay live here. Um So, from you guys while I try to get this rasp out of my voice. Um Any words of wisdom, smart comments Paul that you wanna make or uh anything else? Well, thanks for filling in.
Yeah, I got nothing. OK. Can I brainstorm an idea with you guys? Yes. All right.
So I was thinking about a juice groove and um like a lot of my projects, I, I try to keep them with limited tools. Um And sometimes a juice groove could be tricky if you don't have a jig or if you don't have a plunge router trying to get that. And so, you know, sometimes I do what like additive joinery is what I call it. And I, I was thinking about it. OK?
Most people have a palm router and they would have like a cove bit or a round over bit. So in this case, if you used a cove bit, which is usually included in, you know, like a basic bit set, um And you did a cove bit around your board and then you cove additional strips. Yeah, additional boards. Could you then laminate them around the perimeter of your board? And then that would give you the half round groove.
Would that work? My only concern would be gluing on to the end grain? I think that would be the only, you can't turn the corner right? You can't because you, you wouldn't wanna miter those long grain pieces and wrap the end grain of a whatever 12 inch wide board. Hm.
Um, Alicia, another thought would be to get one of those. Um, I'm drawing a blank but the handheld dremel, the small dremel and get one of those bits and they sell so many bits or the little, the little ones with the sanding head. I mean, it'll take you a little more time, but that can also be an option to create a juice groove. Yeah, I like, yeah, sorry, I, I caught George's raspy voice. You sent it to Arizona?
I know there's gotta be some other way. Right? Like I'm gonna think about that one a little bit longer if maybe, you know, you partially cut the distance on it prior and then I don't know. I'm gonna think about that some more. Yeah.
Carving, you could do it with a carving tool as well if you were a little bit uh forgiving with yourself about, you know, the, the precision of the shape, you know, it might have a little bit more. If I carved it, it would have a little bit more of an organic feel to it. Um, which I, I, I'm kind of ok with, for the most part but uncertain, you know, a more formal looking cutting board. It might not look right. Yeah.
Um Like what sharks got there? The ball, what am I thinking of a bald gouge carver, you know, um, in a drummer or some kind of rotary tool could maybe do it and you could do, it'd be interesting. You could set up a straight edge that, that, that, that could track down. Um, so it would end up relatively straight depth of cut would be a little bit challenging to get that uniform. Um, modify the sandpaper to go over the top, you know.
Yeah. Yeah. That's a brilliant idea. So, I think there's something to that about. Yeah.
Modifying your little barrel. So that only cuts. Yeah. Yeah, that little bird would do it. Yeah.
Well, hey, we've got, um, we got a couple of questions. So, um, Doug says Home Depot and others sell massive thick butcher block countertops and nicely glued finger joints. In addition to boards I made of my own material. Any particular reason I can't salvage a piece of that countertop and use it as a cutting board. Hm.
So I'd have a couple thoughts on that if I might. So this kind of leads into a couple of the more common questions that we get, uh, at go a about cutting boards is foods. You know what glues our food safe and what finishes our food safe. And so I think in the context of a, you know, sourcing something like that, I think the challenges that you have are if it, so you don't know what glue was used so you can send off their finish, but you can't send off their glue. Yes, you could stand off the finish if you had the confidence that you were getting it all.
Uh And, but you can't sand off their glue and you know, it's so there's only, you know, one glue that I know of. That's FDA approved uh as food safe and that's type bond three, there might be others. Uh 202 and three are both. Ok, thanks. I did not know that.
So, uh so, so those are options that are FDA approved for contact with food. Uh Me, most glues are not uh FDA approved for food contact. So, you know, you're kind of rolling the dice there and then you're rolling the dice on the finish as well. Anything else? Alicia Sha what do you think?
No, I agree with Paul. I'd be very careful about re repurposing something that you don't know what it is. Maybe try looking for an unfinished. Um But your block, I know they sell finished and unfinished. You know, that would save you at least the step of having to clear the finish off of it, but one would hope they would use a food safe finish on a countertop.
But you never know. Yeah, industrial glue. I mean, we've all been to IWF in a WFS. It's the industrial side of Luter King is a whole different thing than what we do in our shops. Um Steven says interested in what sort of frame to put around an end grain cutting board.
Should I also use end grain timber for a frame surround the board? As long as, as long grain frames seem to open up cracks between them and the body of the board. So I think that the end of the day here it's make an un grain board and then capture it with a frame. And I think it's also gotta be ingrained, right? Like to keep seasonal movement the same among all the parts.
Yeah. Yeah, we yeah, they're again kind of tying it back to the questions that we get at uh go a one of the more common ones is a picture of something that is uh picture framed and yeah, why did my table crack? And it's, and you can see it coming from a mile away. And uh so you gotta be really careful with, with constraining that wood movement. Uh Doug says interested in how to safely route handles into the end grain of an edge crane board.
So Doug that's covered. Uh We just hit that a little bit in that, you know, looking at some of the videos that we have in the hub for you. So there is a stand alone video that's all about putting handles or relief or whatever I call them. Um hand holds I think is what I call them into the ends of a cutting board. Three different techniques.
Rufus asked on this is about your board. Paul is s is the sap wood softer and then is the board still functional? It is slightly softer if you got in and, and, uh, you know, did a jana test on it. It would test slightly soft, softer. Um, what you'll find with end grain cutting boards though is it's really not going to be a problem that, that end grain has a self healing characteristic about it.
You run a knife through and it just kind of swells back up around it. So it's not, uh, it's not gonna be a problem at all. And I, I was, um, when I was researching the material side of cutting boards, it never occurred to me, but it makes sense and now I'm, I'm also making knives. Um, so this, maybe that's why it really resonated with me that there are woods that are too hard to be used for cutting boards. Like you shouldn't make an entire cutting board out of purple heart because it's so hard.
It really quickly dulls your knives and it's in a couple of the boards in the video, there's strips of purple heart in there and that's ok. Um, but, um, better to be a little bit too soft, don't use pine. Um, but better to have that sap wood in there than to go the other way and have iron wood in there, which is get very quickly dull knife edges. But that is a great question. And and I would not suggest using uh cherry sap wood in particular for a regular long grain cutting board.
It is. I would, I would say that that would be, uh, too soft. I'll just add a little fiber to your, to your diet. Yeah. Yeah.
Yeah, exactly. Um, same as general tips for reducing plane or snipes. So this, I mean, we don't want to fall down a rabbit hole. We've only got a couple of minutes left. But, um, says he's tried aligning in feed and out feed tables using trailing boards, still getting snipe on his cutting boards or her cutting boards.
Um, no, I don't know. I, I either cut her head, maybe a, a cut her head. If a, if the, uh, trailer board is not working, I would say use a wider trailer board that, that should be foolproof. You've got something really wrong if you're using a trailer board of the same thickness, which you sure better be. Uh, you, you bet.
Yeah, you kind of have to be. Um, and you're still getting that, try a wider one. And if it's still happening, then I, I'm really stumped because it really should not happen at that point. I would be curious to know how much, um, that person is taking off if they're taking off too much at a time because sometimes that can cause night. Yeah, it just makes it a lot worse.
Yeah. And then two spanning. So if you've got the table under the cutter head and then in feed and out feed spanning that entire span with one piece of melamine so that you're, you're bridging in feed main table and out feed with one piece. Um That can also help a lot. But yeah, I think Sharks point is good if you're over cutting what your player is capable of that could introduce snipes and watch the grain direction too.
Um And then Sam also asks what kind of clamps were used and what small C So when you get the PDF, um all that stuff will be there for you in the PDF. Um Steven says I've seen curves cut and cutting boards with a template and router with a six millimeter straight cutter. The curve is cut halfway into the thickness and then a flush cut bit used to finish the smooth curve. The inlay used needs to be six millimeter to fill the gap. So, yeah, I think it's just another, he's just pointing out another um more of a routing technique like it's really an inlay where what I'm calling an inlay in mind is not really an inlay, but um an approach for actually producing an inlay.
Um Jamie says I've made juice grooves with my shop, Smith Mark five data blade. It seems to work well. So I that seems funky. I don't know if you mean juice grooves or the handholds on the end, a juice groove with a data blade would be a little interesting, I think, like, because generally they're not a flat U shape. Um, a juice group isn't a flat bottom U shape.
It's a slightly kind cave rounded. He's, he's an out of the box thinker. Yeah. Yeah. All right.
We can get away with a notch too. Right. V notch would work. Ok. You think you could do it with a bit?
Yeah. Um, so one of the cool, I mean, away departure, but one of the cool things about doing it on AC NC is you can tell it to ramp. So you could you see this on commercially made cutting boards where they're shallow on one side of the board and then they're gradually deeper as they get to the other side. Um, you could do that with a handheld router. You'd have to make a ramp for the router to ride on to do that with a handheld router.
But it's a cool thing to a cool aspect of doing CNC work. Um, so we have one more question which works because we're about out of time. If my shop is 55 to 60 degrees, what glue is best? And you're at 55 to 60 when type on Bob was here for the live stream? You're still ok with original or type on two or type on three, right?
Like, um, yep, you're, you're not cold enough to be nervous there yet. They, so they do on the tight bond products, they do not all have the same uh temperature, you know, lower temperature if I remember, right? Uh Tight Bond three is you, you're cutting it kind of close at 55. So Tight Bond three I think says down to 50. And that's the one that is the uh allows the coolest temperature if I remember.
Right? And this is probably 10 years ago when I studied on that. So I might not be right. But look at your product because they, the tight bond products will say a unique idea. Read the label.
Yeah. Um All right. Well, that was our last question. So, um, one I really wanna thank Paul who's there on my TV, my computer and Alicia and Shar for participating in this, this, it's a lot of work to, for them. They not only did the cutting board, but there's a lot of background that goes into this.
And then of course, participating in the live stream that we're doing right now and being part of this, um, challenge to get their ideas in front of you. And I think, I mean, I'd really um encourage everyone, everyone to capitalize uh here in the gift giving season. Look at the cutting boards. Happily steal ideas. Combine ideas.
Um And then two, there's all that how to information back at the cutting board hub that you can use in order to help you get maybe a little more efficient at making your cutting boards. Um, I'll start with you, Paul. Any closing comments from you? I love holiday, woodworking. And, uh, I, I've used cutting boards as my go to for a couple of the seasons over the years.
And, uh, yeah, I just, as you said, I would just encourage everyone to get out there and make some dust this holiday season. All right, Alicia, you know, I like, uh, finding weird materials, you know, I'm the type. I, I don't know. I like to source things a little bit differently. Um, create something new.
So look for different cool things for handles or for legs or things like that, you know, little pieces of hardware or, you know, brass, like I'm pretty sure George you've incorporated brass into some boards before for handles and stuff. So yeah, consider, consider more than just wood possibly for your cutting board. Great idea. All right, Shar, you, you've been like the cutting board queen with your classes the last couple of weeks here or couple of months. I don't know.
But recently on social media, you've been very active with um cutting boards. So what do you got for us? Close us? I'm sure a lot of people are looking at my shop, the shop you guys have and they go, well, of course, you guys can make cutting boards. You got $50,000 worth of tools, but you don't need expensive tools to make a cutting board.
There are options for everybody you can buy, um, the boards already surfaced on four sides from companies like Rockler. So you don't have to worry about a Planer. You don't need expensive clamps. Um, make sure you clean the glue up. So you don't need a planer.
You don't even need a table saw. You can do these things with a circular saw. So just start somewhere. Don't think that you need a lot to make something simple. It's, it's a great point.
And um I, I think Shar might have started out by saying cutting boards are the gateway drug into woodworking for a lot of people, which is true and, and somewhere in this stuff, I say there's kind of an expectation that if you're a woodworker, people expect you to make a cutting board for him, which isn't a bad expectation. It's a great, it's a great way to practice your woodworking skills. Um So the other thing, um you know, a couple of calls to action here, one is um all three of these folks have youtube channels and social media channels. So if you're not already be sure that you look at the documents and you follow Paul and Alicia and Shar on their other channels, um go to the hub and get there are two different PDF S there you can download and then you can watch those five videos to get a little bit more information. And then other than that, um thanks again to you folks.
For taking the time to do this. And um we will see you the next time we do a cutting board challenge. Thanks for watching.
Great video! What solution should I use for the craft stick board so that the die does not fade or bleed? Thx, Dave