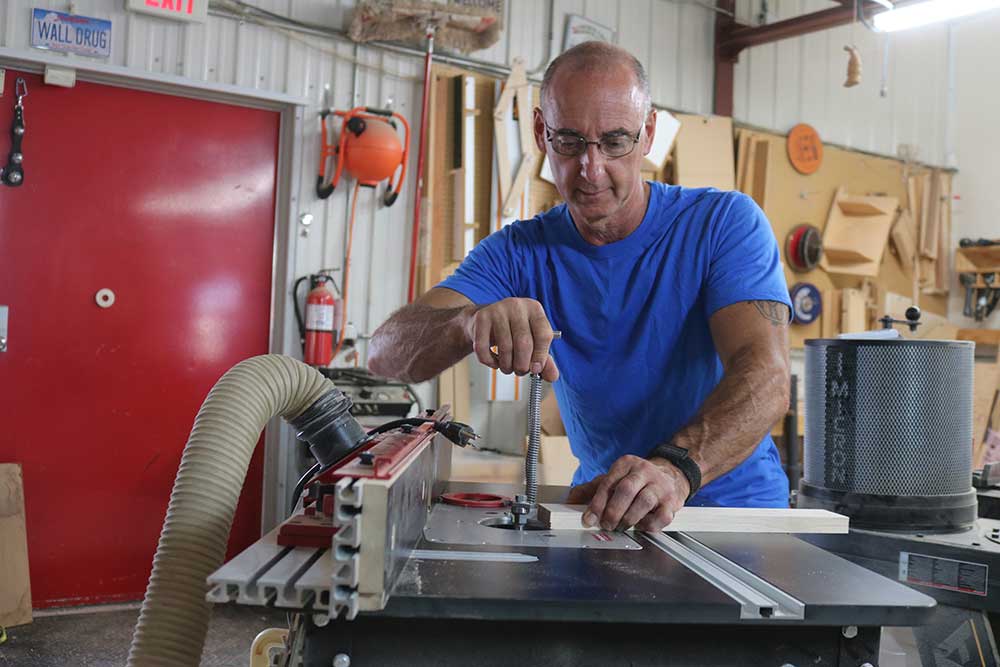
Barnboard Quilt Project
George VondriskaDescription
Barnboard quilts are VERY fun projects. The idea is to make a wooden representation of a traditional quilt square. Historically, some people think that hanging a barn quilt on a building will bring good luck and prosperity. This is a great woodworking project.
The Design
There are lots of options for a barnboard quilt design. You can search the web for quilt patterns or barn quilt patterns (use the images option) and use those as a jumping off point for your project. Or, you can use the plan we provided and build a barn quilt just like the one George made.
Material
Although we’re calling this a barnboard quilt, don’t feel like you MUST use barnboard for yours. The video provides you with other material options.
Bringing it all together
The barn quilt George made will be hanging outside, so it’s held together with Titebond III. We provide you with background on glues to help you make the right decision about what adhesive to use for your quilt.
This, my friends is a barnboard quilt. It's pretty cool. And there's a lot of room here to be creative. So here's the deal. In my case, I am actually using barnboard.
If you don't have access to barnboard, don't sweat it. A little bit later. I'm gonna talk about alternative materials so that no matter what, you can make this. What is fun is to poke around a little bit, look for quilt patterns, steal ideas. And then we're just gonna use wood to emulate the geometric patterns that come from quilt squares.
Now, if you want to just make this one, we're providing you with all of the dimensions that you need to make this particular pattern for yourself. So it's a cool project. And it's something you can hang indoors, you can hang out doors. And I feel like now that I've got one or two of these made, there'll be more of these in my future. So let's get started on this and hopefully I'll get you as excited about it as I am.
First thing I did on this project, really the first thing I did, is look online at images of quilt patterns and at images of barnboard quilts. Because in order to know what we're gonna do with our material, we need to know what this thing is gonna look like. So again, what we're emulating here are real quilt patterns that somebody would stitch together with fabric, but we're gonna get our color contrast, instead of using fabric, by using wood. So spend some time online and look at images of quilt patterns and barnboard quilts, because you're gonna need to have an idea in your head of the geometrical design that you're gonna use. So, I've already done that.
Got an idea of what I want to do. The next thing I did is I sorted my barnboard so I could see how much red, how much white, how much natural I had available in order to know, can I make the pattern that I want to make? My quilt is gonna be, my quilt square is gonna be 24 by 24. So yes, I have enough here in order to do that. I keep calling this a barnboard quilt, but don't sweat that.
If you don't have access to barnboard or you just want to go a different route, another way to do this would be just to use woods that have their own natural differing colors. So in this case, maple, red oak, walnut. If we add cherry, we'll have another color. If we have pine, we'll have another color, add pine, we'll have another color. If we had purple heart, you'll have another color, paducah.
So you could simply use wood, and with a variety of species you would get a variety of colors and use that to create your pattern, instead of using barnboard. That's fair game. Another thing you could do is use plywood or solid wood, and you could stay in it, leave it natural, use aniline dye. Aniline dye, that's what that blue is, it'll provide a really vibrant color. And you can get red, blue, green, yellow, brown.
So aniline dye would be another great way to go, either on a plywood, like I've got here or on solid wood to get the color contrast that you want. So don't feel like you're painted into a corner by being required to use barnboard for this. So for me, I know what my pattern is gonna look like. I know how big it's gonna be. My next step is gonna be to head of the table saw and start getting my barnboard ripped into the strips I need to create my pattern.
If for your quilt pattern you're gonna be using just wood, like pine, maple, oak, walnut, cherry, to get your color contrast, you'll be able to simply joint an edge on the material and then rip to the widths you need here on the table saw. If you're using plywood, your approach might be a little bit more like what I'm about to do. With plywood, what I would do, is stain or paint large pieces of plywood, then go back and rip the strips out of them. I think that's easier and faster than ripping all the strips and painting or staining each individual strip. Kind of like where I'm at right now with the barnboard.
The barnboard has another wrinkle to it, which is, on a lot of the pieces the edges are kerflooey. So, if I leave this edge on here, and then I go to marry it up against another edge, what's gonna happen is that those two aren't gonna marry together well, they're not gonna close the joint. So, what I need to do is do one rip where I help straighten that edge out, or I could do this on the jointer, and then I'll start ripping to my final width. So to make this happen, to make this go a little bit faster and easier, I put a straight edge against the table saw blade, with the saw unplugged, and with a felt tip I made a line on the table. So now when I come along with this piece I'll have the guard down, I'm leaving it up for now so you can see, and with the guard down I'll be able to slide this over until I can see, on that felt tip line, that I am in fact gonna make a cut and then push this piece through to get that first straight edge.
Set that one aside, grab another one, do the same thing. So this line on the table, basically, that's the saw blade. It represents the saw blade and it lets me find that cut 'cause it's gonna be different for every board, without having to get the guard out of the way, without having to measure. The other thing to be cognitive of is that we don't know anything about that barnboard. We don't know what kind of paint is on it.
We don't know what kind of, I dunno, dust is in it. So I'm gonna wear a respirator helmet as I do this to make sure that, in addition to the dust collector, I'm protecting my lungs here and I'm not inhaling anything gross off the barnboard. Final thing there, make sure there are no fasteners in that stuff. I don't want my table saw blade to find them. All right, here's how this will look.
Dust collection. I'll get my respirator on in just a second. But with the guard in place, get against my fence, slide over until the edge of the material is hitting that felt tip line. And then I'll go ahead and make that cut. And really here we're just in a rinse and repeat mode until you have enough strips to make all your parts.
And they don't have to all be the same. So my particular design, everything is two inches wide. But it could be varying widths to add some more visual interest to what you're doing. So this step, get all your parts ripped to size. And we're pretty close to putting our quilt pattern together.
Before we start putting pieces together here and making our quilt pattern, let's talk about a couple different things. First, the backer board. Mine is gonna live outside. So it's important that I pick the right glue. We'll talk about that in a second.
It's also important then that the backer board can live outside. So in my case, I'm using a product called MDO. It's commonly used by sign makers and it's fully exterior. So if you're gonna be outside, exterior grade product for the backer board. If you're gonna be inside, it could be any kind of plywood, particle board, whatever you want to use.
I'm using 1/2 inch like stock for mine. Now, let's hit on that adhesive idea. We've got a couple of things going on here. If it's gonna live outside, then we should use an exterior glue. So I'm just gonna go with Titebond III for this.
Titebond II would do it because this is gonna be damp not dripping wet all the time, like a planter. But, if I go with III, it's a little more insurance because it's waterproof more so than water resistant. So again, either one of these glues would work for outside. I'm gonna go with III. Now, also, if you're gonna be outside, you could go with polyurethane glue.
Polyurethane is gonna also offer the advantage that if you want to throw some little material curve ball into this project, polyurethane glue could be a good way to fasten it. So for instance, I'm working with porous materials. I'm working with barnboard for everything. It could be really cool to put in a strip of solid surface countertop or maybe a little brass piece or something like that. If you want to adhere those to your backer board, polyurethane glue is gonna take care of that.
And it's exterior. If your quilt is gonna live inside when it's done, then you could use conventional yellow glue for the whole thing. So choose your backer, choose your adhesive, based on your application. Now, on the backer, a little bit of work has been done. For my particular pattern, I need to have some layout on here.
This and this are like X and Y. This is the center of the board in this direction. This is the center of the board in this direction. Then I also need to have the diagonals marked out. And then when I start putting my parts on that's gonna help me get them in the right spot.
When you're cutting your parts, a couple things here. Use a miter saw, the easiest way to go, or a miter gauge on your table saw. So ,the way to do this is to cut one end. And then use a stop block so that when you push the cut end up against the stop block, all of your parts are gonna come out to the same length. One of the things to recognize is that in order to get the mirror images that we need to make most of this pattern, 'cause it's symmetrical about the center, so we have a left and a right, you're gonna cut some of your parts with the painted face up.
You're gonna cut some of your parts with the painted face down, so that we end up when we're done, a left and a right, so we can start putting this together symmetrically. At that point, what you can do is get going on cutting your pieces. And next step, we'll be able to start gluing them down To start putting this together, what I would do, even if you're following my pattern and using that cut list, I would only cut the parts for this center core to start out with. 'Cause once we get these on, then you could measure to see exactly how long does this piece have to be to finish the pattern out that way. So, don't work off the cut list and cut everything.
Just start, we'll do this in increments that make sense. Now what I'm doing on my end is I'm putting the point here, of the arrowhead, right on the center point of the jig. And then on that end, I want to make sure that joint is on that pencil line. That looks great. And at the end of the day, it's the glue that's gonna hold everything together.
But while I'm working around this, I don't want to take a chance of disturbing it. So I'm gonna use a 23 gauge pinner and just a couple of pins in each one. And that'll hold it while the glue dries. And then it's just a continuation from here of doing the same thing. Notice that I'm not pinning those.
I'm gonna get the rest of this kind of pinwheel center all on the board. And that's just so that if I need to kind of shift stuff around a little bit, I'll be able to do it, 'cause I don't have pins in it yet. All right now, with everything here, you could look and see, do I need to, I don't know, move this around the clock a little bit? Is it good the way it sits? Do I need to make any adjustments as I go?
And I'm gonna say, I'm pretty happy with that. So pin away. And then what you can do is figure out this next part. 45 degree cut on this end, square on this end. How long does it have to be to finish that out?
One of the things to recognize is that even though we're carefully cutting parts, I'm not asking all of these mitered cuts to close perfectly. We are dealing with barnboard. So there's gonna be some imprecision, some lack of precision that's inherent with working with this stuff. So if it's a little bit gappy in there I'm not going back and re-cutting pieces. These last pieces are really small and your best bet will be cut those little triangles with a handsaw instead of with your miter saw.
Last step, putting a frame on. Now, depending on what you use for your backer board and how thick your quilt material is, that's gonna affect the size of the frame. So, pay more attention to your project than my cut list. I made my frame 1/4 inch wider than the combined thickness of the backer and my barnboard. And I'm using a brad nailer now instead of the 23 gauge pinner.
'cause I wanted to have a little bit bigger brad going. and all I'm doing is cutting these pieces to fit and then pinning it with glue of course, like before. The brads are just little clamps holding this until the glue grabs it. And with that, that wraps up our barnboard quilt. So, I think it's a pretty cool project.
And what I liked about it was the creative side of messing with the colors, messing with the pattern. One thing to keep in mind here, especially if you're working with barnboard, is don't split hairs over little bit of gap-icity. If you've got some gaps between the parts it's gonna be the nature of the beast of working with this rougher material. So cut yourself a little bit of slack on the joinery there. I'm really happy with how this one came out.
And I hope you enjoy making yours as much as I enjoyed making mine.
Very cool idea. I live in an old farm house and this gives me a great idea for a cutting board based on your design. Thanks
In your dimensions for the barnwood quilt shouldn't C be the same dimensions as A? LTS? I apologize if I am confused. I'm going to try this with different species and different thicknesses.
What is the dye you reference. Is it anoli dye or anolin dye?
Very nice project!